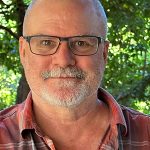
Building Support for FMEA with Fred Schenkelberg
We’re glad to have Fred Schenkelberg from the Accendo Reliability website joining us. He hosts the Speaking of Reliability podcast and even does reliability webinars. Fred also has articles and helps create online courses on Accendo. He’s well versed in the product development space of reliability engineering. But among the tools used, he’ll give us an in-depth look into gaining support for FMEAs.
Fred will give us insight on:
- Are organizations willing to give up their resources?
- What can you do to gain support for FMEAs?
- Top points for building support for FMEAs
… and so much more!
Are organizations willing to give up their resources?
No, they aren’t. It’s easy to tally up the cost. Some staff members are expected to do more than their duties due to limited resources and time. To meet deadlines, everything needs to keep flowing. That’s why organizations aren’t willing to spare resources as the cost is immediate. Giving without having a clue of the returns is a risky proposition. This element is present in different industries.
With FMEAs, there are a lot of amateurs trying to do the job. Yet, even with an idea of what’s expected, execution is usually poor. That’s part of the reason people steer clear from FMEAs. There are several barriers embedded in our cultures. The most prevalent are change and past experience. You also need to take into account where the FMEA will get used. Extra barriers will come up. It brings about the reality of failure, and few people like that topic.
What can you do to gain support for FMEAs?
The easiest way to gain support is by doing it rather than asking and waiting for approval. Set up meetings without mentioning they’re about FMEAs. When you’re in there, discuss:
- How things could fail
- What are the issues?
- What are the modes?
- What happens more often than not?
By asking all the right questions, you can still do an FMEA. But it’ll take a lot of work, and it is no longer convenient. You also don’t get the level of synergy that comes with having everyone in one room. But this arrangement enables you to start the process without resistance. If you can talk to a few people, focus on the top issues. Then explain why they’re important and what you plan to do, and the support will come.
Mention that you’re working on high severity and high-frequency things. This will explain the purpose of the questions you ask. You can then define the possible savings in detail. From there, you can start building a small team with experts from different areas on the floor. That will help you focus on various departments as the need arises.
Some companies allow their members to experiment with FMEAs. That’s to a point where they even give funds for the process. But if your company doesn’t, then start small and track your results. Based on your findings, you can make a case on the importance of an ongoing FMEA program.
This would work well if you’re leading a team. The informal FMEA would provide you with the tools to resolve arising issues with your team. Then other departments would get to see your progress and show interest in your process. You can then outline your Plan-Do-Check-Act process.
Another way to do it is by saying you need other departments involved. With that, you’ll need to call it an FMEA to get the required funding. Ensure the person knows what they’re doing as a facilitator to ensure you get value from it. This method makes it harder as you need a high-ranking person in the company to support the use of resources.
But, the most effective method is having a track record that works. Then mention that expanding across groups would work even better. So, start small so that you can practice how to facilitate in a safe space.
Unfortunately, the informal method loses a key value of the FMEA. It’s still there, though not as usual. That’s the cross table talk. Those involved should have an open mind and take part. You’ll get to see the various challenges different teams experience. That’ll also help each department understand which area needs to get prioritized first. This process proves to be as valuable as the analysis itself. From there, you can quantify how much of a difference the FMEA made.
The company should, however, realize that an FMEA process cannot always get done. It creates the right tool to solve a given problem. It doesn’t sort all issues that could arise within an organization. So before deciding you need an FMEA, think through what the benefits of using one would be. If you already have a list of priorities, the FMEA would only help confirm that. Thus, it would be pointless to do one.
Top points for building support for FMEAs
- Start small and build a case history for success
- Actively connect the tools in FMEA to what makes a difference
A measure of your success in getting support will be when you automatically get support for FMEA meetings. The team you need won’t feel the need to come up with excuses to evade attending. The tipping point is when you have enough of a culture and enough people saying an FMEA is a useful tool.
There’s plenty of procedures and standards written on how to do FMEAs. But only a few of them mention the questions you should answer before calling a meeting. They include questions like:
- What are the criteria to do this?
- What are the signals that it’s a useful tool for your current situation?
These are missing from many organizational documents. You should always include the criteria of when and why you do FMEAs.
Eruditio Links:
Fred Schenkelberg Links:
- Fred Schenkelberg Linkedin
- Accendo Reliability
- Speaking of Reliability Podcast
- Effective FMEAs by Carl Carlson
- Basics of FMEAs
- Inside FMEA articles
- FMEA resources
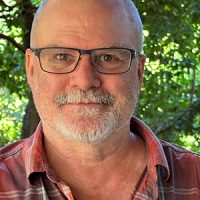
- Social:
- Link:
- Embed:
Rooted In Reliability podcast is a proud member of Reliability.fm network. We encourage you to please rate and review this podcast on iTunes and Stitcher. It ensures the podcast stays relevant and is easy to find by like-minded professionals. It is only with your ratings and reviews that the Rooted In Reliability podcast can continue to grow. Thank you for providing the small but critical support for the Rooted In Reliability podcast!
Leave a Reply