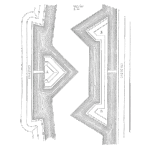
Understanding and Controlling Process Variation
Let’s discuss sources of variation and how to measure, monitor, and control processes to minimize the differences from one part to the next.
Statistical process control (SPC) is a set of tools that provide insights into the changing nature of processes.
Product designs include the design engineer’s desired dimensions and an allowance for variation. Engineers use tolerance analysis to determine a range of sizes to enable assembly into the final product.
If every component complied with the design’s nominal values without variation, every assembled product would work as intended. Unfortunately, components, materials, and parts vary. They vary within or beyond the design specification because the variation directly results from the processes that create the part and not the design intent.
Manufacturing processes create parts that are different from one another. Even a well-controlled and stable process has variation.
When the design calls for restricting the variation with a tolerance smaller than the natural range of variation, parts will still have dimensions outside the specifications. Manufacturers may include an inspection to sort out faulty parts, thereby incurring higher yield losses and higher costs.
Some ‘out-of-spec’ parts might only be found after assembly into a final product, compounding the cost of the error. Where is the root cause of the out-of-spec parts? What element of the process led to the faulty product?
When the design does not account for the normal variation of the manufacturing processes, it is inevitably the designer’s fault. Variation happens.
In this webinar, we will discuss the various sources of variation and how to measure, monitor, and control processes to minimize the differences from one part to the next.
Statistical process control (SPC) is a set of tools that provide insights into the changing nature of processes. Making variation visible allows the entire team to minimize excessive variation.
Even if we accept that no two parts are the same, it is not safe to assume that all parts are within the expected or defined range of values.
A process that is not monitored or controlled will generally create results with excessive variation.
This Accendo Reliability webinar originally broadcast on 14 June 2016.
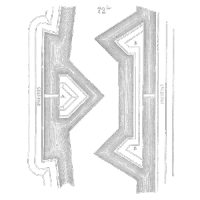
- Social:
- Link:
- Embed:
To view the recorded webinar and slides, visit the webinar page.
Related Content
Design Specs vs. Process Control, Capability, and SPC episode
A slew of articles or tutorials on SPC and Process Capability
When should SPC be used? article
Why Understanding Statistical Process Control Is Important article
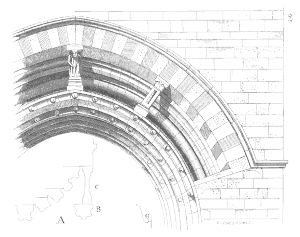
SPC Sample Size Impact on SPC
In this webinar, we explore the impact that chart selection and sample size have on chart sensitivity (the ability to detect changes).
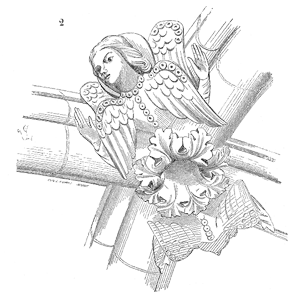
Reliability and Statistical Process Control
Let’s explore some cases where effectively using statistical process control will enhance your product’s reliability performance.
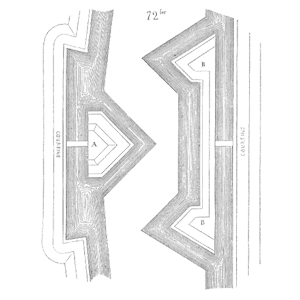
Understanding and Controlling Process Variation
Let’s discuss process variation and how to measure, monitor, and control processes to minimize the differences from one part to the next.
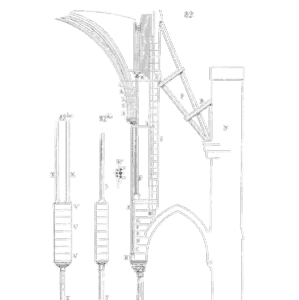
10 Keys for Maximizing the Benefits of Your SPC Program
Progressive manufacturers use control charts to “listen” to their processes to detect and rectify potentially harmful changes.
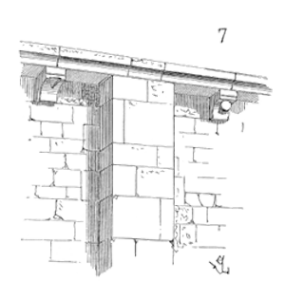
How do I link Process Capability Indices to Number (PPM) Defects?
if you need to learn a bit more about manufacturing and how we measure quality in general? Join us for this webinar.
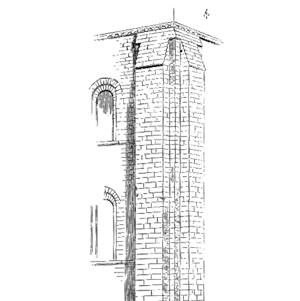
What is Statistical Process Control or SPC?
You may have heard of Statistical Process Control, 6-sigma, Shewhart, the Japanese Economic Miracle, X̅ – R Charts … or perhaps none of them.
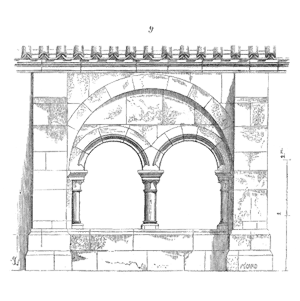
What is Process Capability Analysis (PCA)?
A process is considered ‘capable’ if it creates products that, with production natural variation, are still within what ‘good’ looks like.
Leave a Reply