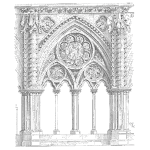
An Introduction, Basic Steps, and Examples of How FMEA Goes Wrong
Failure mode and effects analysis (FMEA) starts with brainstorming and ends with prioritized actions. A great tool to get your team thinking about system failures. Let’s explore the fundamental steps and beset practices to get value from your analysis.
You may hear moans and groans when you suggest the team participate in an FMEA. Sometimes, the analysis is tedious, and sometimes, it provides little actionable results.
Your task when facilitating or participating in an FMEA is to help the entire team employ the tool to improve the team’s ability to achieve the customer’s expected reliability performance. You can help make the FMEA process useful for all involved. You need to know the fundamentals of FMEA and a few best practices to succeed.
Let’s review the basic steps for any FMEA, plus how the FMEA process is best set up for success. Plus, let’s expose a few very poor practices that eliminate value from the process.
The discussion will focus on the flexibility of the FMEA process, plus the hints and tips to get past the potential rough spots during the analysis. Bring your experience, best practices, and questions to this discussion about FMEA.
This Accendo Reliability webinar originally broadcast on 11 April 2017.
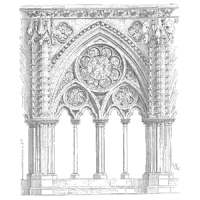
- Social:
- Link:
- Embed:
To view the recorded webinar and slides, visit the webinar page.
Related Content
FMEA Resources page
Where are FMEAs (and their standards) Heading? episode
How to use FMEA for Complaint Investigation episode
Reliability Predictions and FMEA Occurrence episode
FMEA Occurrence Question episode
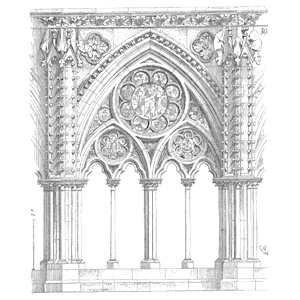
Fundamentals of FMEA
Just the fundamentals of FMEA in this fast paced event. FMEA has value, the 10 steps, and a few examples of how it can go all wrong.
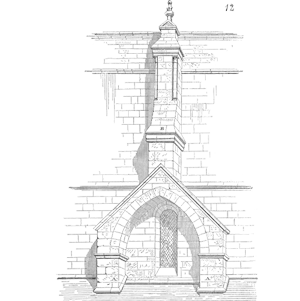
10 Reasons to do FMEAs
Exploring ten reasons to do FMEAs, yet actually, reasons to do amazing FMEAs that provide value in a range of ways.
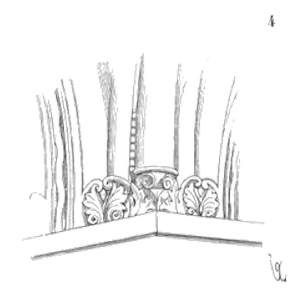
Supportability (and FMEAs/FMECAs)
What is ‘supportability?’ Easy! It’s the ability of your product, system or service to be supported. But how do we get this so wrong so often?
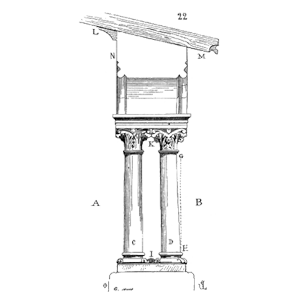
What is the difference between Design and Process FMEAs?
Get an overview of which FMEAs do what and when you would use one instead of the other? Including Design, Process, and others.
Leave a Reply