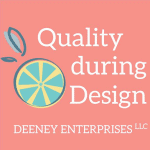
Try this Method to Help with Complex Decisions (DMRCS)
Your team is faced with a complex decision. Maybe it’s complex because you have a lot of options or maybe it’s complex because it’s technically challenging and requires some testing. You may want to consider a structured approach: DMRCS.
- D – Define – What are we trying to accomplish? What are our choices, including not acting?
- M – Measure – What metrics are we using to measure our choices against our goal and against each other?They should be precise, consistently applied, and fair.
- R – Reduce – Start narrowing in on the solution. Check: do our metrics and choices match up with what we’re trying to do? Output meaningful, worthwhile solutions.
- C – Combine – Combine metrics to better understand the trade-offs of options
- S – Select – Make a choice
Just like six-sigma’s DMAIC, the Define and Measure parts are the most important.
If you or your team are finding you’re stuck in making a complex decision, try a structured approach to solving the problem. DMRCS may help your team find that structure so you can make informed decisions with high quality data.
A Pareto Front Example
Citations
These articles were published in an ASQ magazine, Quality Progress. You do not need to be an ASQ member to access them (they’re free), but you do need to register on their site.
I quote Dr. Anderson Cook in the podcast from this article:
Anderson-Cook, Christine M. “Let’s Be Realistic: Strengthen Decision Making with Formal Structure.” Quality Progress, Mar. 2013, pp. 52-54.
The DMRCS model is presented in this article, with an example of choosing a job for employment.
Anderson-Cook, Christine M. and Lu Lu. “Much-Needed Structure: A New 5-step Decision-Making Process Helps you Evaluate, Balance Competing Objectives.” Quality Progress, Oct. 2015, pp. 43-50.
See this article for another example of tools, based on a decision on which supplier to choose. These tools are highlighted: Pareto front, trade-off plot, mixture plot, efficiency plot.
Anderson-Cook, Christine and Lu Lu. “Weighing Your Options: Decision Making with the Pareto-Front Approach.” Quality Progress, Oct. 2012, pp. 50-52.
Episode Transcript
Your team is faced with a complex decision. Maybe it’s complex because you have a lot of options or maybe it’s complex because it’s technically challenging and requires some testing. You may want to consider a structured approach. I’ll tell you more about DMRCS after this brief introduction.
Hello, and welcome to Quality during Design, the place to use quality thinking to create products others love for less. My name is Dianna. I’m a senior level quality professional and engineer with over 20 years of experience in manufacturing and design. Listen in and then join the conversation at qualityduringdesign.com.
We make decisions every day. What do I want for breakfast? How much should I pay on that bill? Should I answer this call or will it be about an extended car warranty that I just don’t want? If we’re successful at adulting, then we’ve gotten pretty at making decisions. But what about making decisions with a team of people at work? Do we make good decisions based on information and everyone’s input, or do we make gut reaction decisions? Maybe we’re not confident that we’re good at it at all. Is there a quality tool that can help us provide some structure to our decision making so we can make the best decisions? That’s what Dr. Christine Anderson-Cook and Dr. Lulu were thinking. They both have doctorates in statistics. They propose a system of decision making called DMRCS short, for define, measure, reduce, combine and select, and it’s modeled after the six Sigma DMAIC. The quality profession offers lots of tools like this made to help teams of people solve problems, either solve them for good or for continuous improvement.
Think of the DMAIC, define measure, analyze, improve, and control, and the eight disciplines or eight D. These are both structured models to help teams of people solve a problem for good. They’re linear models. We also have PDSA and PDCA, plan do study act and plan do check act. These are structured ways that we can solve problems for continuous improvement. They’re cycles that we repeat to get better. And there are others. These models and systems have been used by many people over many years with success. And there’s a reason that they’re still around and being taught today. Applying this kind of structure to making a decision makes sense.
This model is for making decisions, not solving problems. So, there are a few twists. This model could be used to make decisions such as, “Which supplier should we use?” We have options for how we want to run our experiment. Which options should we choose to get the maximum benefit out of the activity? Dr. Anderson-Cook and Dr. Lu Lu published articles showing how this model could be used for investment strategies or for choosing the best fitting job for employment. When the decision we’re faced with making involves objectives that are competing, or if there are multiple criteria that we can base our decision on, it makes things complicated and trying to reduce the decision into something binary like yes or no/pass or fail, we can lose a lot of the nuances about the decision details that could affect the end result and not give us what we really want in the end. Dr. Anderson cook described the DMRCS model as a “structured understanding of competitive choices”.
Let’s step through the acronym and talk about what each step would involve. D is for “define” and that’s really when we’re setting the goal of our activities. What is it that we’re trying to accomplish? What is important and what are we able to choose from? What are our choices in this step? I think it’s important to remember that not doing anything is a choice. In evaluating the costs and benefits of ‘not doing anything’ could be beneficial also and provide some impetus for the team to take action. M is for “measure” where we’re choosing what kind of metrics, we’re going to use to measure our different options and compare them against each other. It’s best to have quantitative data here, something that is numerical, that we can measure and perform analysis on. We need to define metrics that are precise and consistently applied across all the options in a fair way. These define and measure steps are very similar to the six Sigma methodology. And they’re also probably the most important of the process. If we don’t adequately define what our scope and what our issue is, and if we don’t have good measures and metrics with which to compare options, then it negatively affects the whole process. And we may end up making a decision that is not good. For a team to spend time on this and get it right the first time is very important.
The next step of the DMRCS process is R for “reduce”. Now that we’ve given some real thought and input into the define and measure stages, we want to be able to start narrowing in on the solution by eliminating either some of the metrics that we just picked or some of the options that we’re considering. We check that the criteria that we just defined is aligned with our primary objective. We also compare our choices against the primary objective. If our metrics and our choices don’t match up with what we’re really trying to do, then we’re going to eliminate them and reduce our options. We don’t want to eliminate options just for the sake of eliminating them though. Our output of this step is meaningful, worthwhile solutions.
The next step of this decision-making model is C for “combine”. We want to combine the different metrics that we’re looking at so we can better understand the trade-offs of our options. In looking at the metrics we’ve defined, which ones are the priorities? Which ones do we value the most?
The last step in our process is S for “select” where we’re actually making a decision. Our input into this last step is a list of prioritized solutions. Now we compare them and select a final choice. Important questions of this step are which solution is best given my priorities? How does this solution compare to other options, and can I defend my choice? We want all of our team to be on board so we’re going to get team agreement. And our decision is going to be able to be justified with the high-quality data that we’ve collected and analyzed.
Dr. Anderson-Cook, and Dr. Lu suggest different statistical methods to apply to this process, to help with the decision making. The types of methods they use are a pareto front (which is a scatter plot that shows optimum choices), a mixture plot (that applies weights and compares different options). A trade off plot and an efficiency plot are also graphical methods that they use to help visualize the options and their criteria. I’ll include citations to their articles so that you can look up these examples and see how they use these statistical methods and graphical plots for yourself.
Dr. Anderson-Cook warned about some assumptions when using this model in one of them, I’m just going to read from her article. She says, “Sometimes even the best decision making can yield an undesirable outcome. In the post-decision assessment, try to separate the outcome from the process of making the decision. Sometimes you are just unlucky, but this should not negate the fact that you followed a sound process to make the decision. The opposite also is possible. You can see a great outcome despite a non-thoughtful process, but you shouldn’t always count on this working out.”
What’s today’s insight to action? If you or your team is finding you’re stuck in making a complex decision, try a structured approach to solving the problem. DMRCS may help your team find that structure so you can make informed decisions with high quality data.
Please go to my website at qualityduringdesign.com. You can visit me there, and it also has a catalog of resources, including all the podcasts and their transcripts. Use the subscribe forms to join the weekly newsletter, where I share more insights and links in your podcast app. Make sure you subscribe or follow quality during design to get all the episodes and get notified when new ones are posted. This has been a production of Deeney Enterprises. Thanks for listening!
Leave a Reply