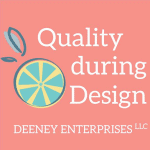
ALT vs. HALT
Reliability engineers may suggest environmental stress tests. There are many types of tests in an RE’s toolbox. We compare two types of commonly known tests that are used for design: ALT vs. HALT. What are the important distinctions between these two methods? What value do they each bring to design engineering? And how do they fit into other reliability test methods?
There are many uses for reliability tests, but they have different purposes.
ALT is Accelerated Life Test
It’s used for quantitative data and for estimating the real-use reliability of a product.
To remember ALT, think of driving our automobile off road, an alternative to pave road, and we’re going to measure the damage afterwards to estimate how tough our car really is.
HALT is Highly Accelerated Life Test
It’s used for qualitative data to highlight areas for improvement.
To remember HALT, think of a car crash test: we’re highly accelerating our car toward a wall to halt it, and then seeing what failed.
(Car crash tests can also be used with sensors to collect data, but this is good way to remember the differences of HALT compared to the other reliability tests).
Citations
Further explore these topics from these other QDD episodes:
HALT! Watch out for that weakest link
Results-Driven Decisions, Faster: Accelerated Stress Testing as a Reliability Life Test
Environmental Stress Testing for Robust Designs
Getting Comfortable with using Reliability Results
5 Aspects of Good Reliability Goals and Requirements
Want to learn more about car crash tests? Or just want to watch cars getting smashed?
Attribution of pictures at the end of the video:
car crash dummy
Airbag vector created by brgfx – www.freepik.com
off roading
4×4 photo created by teksomolika – www.freepik.com
Episode Transcript
You’re listening to an installment of the Quality during Design “Versus Series”. In this series, we’re comparing concepts within quality and reliability to better understand them and how they can affect product design engineering. We have eight episodes in this series, which means we’ll be reviewing at least 16 topics. Let’s get started. Hello and welcome to quality during design the place to use quality thinking to create products others love for less. My name is Diana Deeney. I’m a senior level quality professional and engineer with over 20 years of experience in manufacturing and design. Listen in and then join the conversation. Visit quality during design.com and subscribe.
Hi, welcome to Quality during Design for products others love for less. I’m your host, Diana Deeney. Today, we’re comparing ALT and HALT: accelerated life testing versus highly accelerated life testing. And really what we want to talk about today is environmental testing that a reliability engineer might recommend for our product. Why would a reliability engineer recommend environmental stress testing? Well, there’s a couple of reasons. One is that they want to be able to test the product and understand its reliability before it’s been used in the field, before our customers start to use it. The other is so that they can help us make informed decisions about the design. The results of these tests can also help designers with a lot of design decisions. Things like choosing components. This component might be cheaper. Is it just as reliable? And does it matter in the grand scheme of the whole system? Evaluating suppliers: is there a difference between components or systems or assemblies or even manufacturing methods between two different suppliers? And for our own manufacturing methods themselves: are they able to produce the reliable components that we need?
Reliability engineers, in order to design a test, they need to know a few things. They need to know how this concept or product is going to be used. The environment that it’s used in and – think of temperature, humidity, and vibration – all of the environments in which our product could be used. And they at least need to know the basic concept and layout of the product design. Now we’ll know these things, or at least come up with a good estimate because they’re an important input into our design.
There are a lot of different techniques reliability engineers could use to test reliability of systems and components and of products. And they’re used for different purposes. Some tests are qualitative where we’re testing to a failure and some tests are quantitative where we’re measuring the stress and life of a product. Still other test methods are meant for screening product from manufacturing and determining if there is a shift from a special cause.
Today, I wanted to discuss two particular types of reliability engineering tests: ALT and HALT. And the reason is that these terminologies seem to be more widely known than some of the other reliability engineering tests. They’re both done to help make design choices and not necessarily monitor manufacturing. But they have different purposes and deceivingly similar names. So let’s break down the differences between these two types of reliability engineering tests.
ALT is short for “accelerated life test”, and this is a quantitative type of test it’s collecting data and information about the stress and the life of a product. The goal of ALT is to correlate those stresses in test with reliability and real use, to determine an acceleration factor and fit a probability model. Reliability engineers could just perform a regular old life test, but it might take too long. So they accelerate the stresses that would normally be seen in use in order to get failures faster. The acceleration factor and the probability distribution model are what allow the reliability engineers to transcribe that accelerated data into what they think will happen in real use. This data can be used to calculate the reliability of products, and it’s a demonstration of the reliability because you’re actually testing the product. The results of these tests could be used for verifications and qualification tests and also warranty analysis and where out analysis. These results could show us that the component or the system or product that we’re testing is good enough to be used in the field, or maybe it’s not. We may still get failures that we can investigate for design changes.
The stresses applied during accelerated life testing are usually accelerated usage rate or an overstress. As an example, I went to a home store, Ikea, and they had chairs in a test room and there was a weight being dropped on top of the chair consistently. And that was to simulate somebody getting up and sitting down in the chair several times. Now in real use, someone may only sit in the chair maybe three times, but they were accelerating the test by having a weight drop onto it 30 times a minute. This accelerated the usage rate of their chair. A life test using over stress is applying a stress that is above and beyond what the product would normally see in real use. If we’re designing a part for an airplane, there’s going to be vibration, then we’re going to test it at vibration rates that would be above and beyond what would be seen in the airplane. Stresses during accelerated life testing are also usually applied uniformly and consistently. The acceleration factor is picked based on the unit under test and its use cases, ’cause remember we want to accelerate our tests, but we’re still simulating real use environments. And the accelerated life test time is also correlated to customer use time.
HALT, on the other hand, is a qualitative test to destruct. We’re not going to be able to use results from HALT to simulate real use conditions or develop probability models to be able to calculate or estimate the reliability of something. Instead, we’re testing to a limit or we’re testing to desct. HALT is typically a test to destruct. HAST, or highly accelerated stress test, is usually a test to a limit. The goal with HALT is to rapidly find probable failure modes and vulnerabilities in our components or systems and to help design future tests. The results of HALT may be used in downstream tests for manufacturing audits or stress screens.
HALT is usually not a once-and-done test. It’s usually done, we break something, we investigate the failure mode and find the root cause, design it out or eliminate the source of that cause, and then maybe we might test it again and find out what more vulnerabilities have come up. And these corrective action cycles could be about the design or about the manufacturing process. HALT results also assure a design margin between the specs and the operational limits or the operational limits to the destruct limits. The stresses applied at HALT are usually non uniform combinations (things like step stress or rapid acceleration). And the acceleration factors are unknown. It’s said that acceleration factors could be as high as 2,500. And HALT results are not correlated to customer use time.
Now to put HALT into some more perspective, HALT is not the only qualitative environmental test that a reliability engineer has in their toolbox. There is environmental stress test, EST, which is very similar, but it’s just not highly accelerated. The acceleration factors aren’t on the order of thousands. There’s STRIFE (or life-stress or stress-life, if you’d like): those are also an overstress test, but the stress profile is just below the designed operating specs.
There are also different reliability engineering test methods that have to do with inspection and manufacturing. being able to monitor the products, coming off the manufacturing line to make sure that the process is still in control. These methods don’t damage the product. And it’s either done on all products or treated as an inspection of a few. Some examples of these stress testing for manufacturing are things like burn-in, where we’re essentially wearing in a product through an any initial fallout failures – removing the lemons, o to say. Environmental stress screening uses mild stresses with complicated stress profiles. And highly accelerated stress screen is similar except it uses highly accelerated stresses. There’s also some thing called HASA, highly accelerated stress audit which is another version of a highly accelerated test for inspection.
In all of these, the tests are designed to be able to give us data and information about our product, to be able to make wise decisions. And they all apply stresses to our product like temperature, humidity, vibration, power, and voltage. These are all typical stresses that are applied at stress screens, stress audits, and stress tests. Sometimes reliability engineers need to do some exploratory testing to find out what stresses have the most effect.
So reliability engineering testing isn’t usually just a once and done test. It’s a buildup of knowledge over time about a product and its processes. The information and things we learn about tests that were performed on the concept product are filtered through to the rest of the design process and affect the types of tests that reliability engineers may want to perform later on in the development.
So what’s, today’s insight to action, with ALT versus HALT? Well know that there are many options for reliability engineers to help with product design, even starting at the very early concept phases of product development. The test design itself can tie back to risk-based decisions and reliability engineers consider the use cases of the products in the field when they’re developing tests. What you may learn is that you may need to change a component, reconfigure an assembly, try a different concept, or change how you’re making it. So getting reliability engineers involved early in the concept development is important. You’ll also be able to use the results of tests for due diligence and evidence that your product is safe and dependable before you ship it to the customer.
To remember the differences between ALT and HALT, we can think of an automobile. If we take our car off-roading into mud and sink holes and a big mess, then we may be performing ALT. We’re driving our car through an alternate road course, and we’re measuring the damage that could happen to it afterwards. If on the other hand, we’re loading up our car with crash test, dummies, driving it at high speeds toward a wall so that it crashes – well, that’s more akin to HALT: we’re highly accelerating our automobile until it crashed and halted.
If you like the content in this episode, visit quality during design.com, where you can subscribe to the weekly newsletter to keep in touch. This has been a production of Deeney Enterprises. Thanks for listening.
Leave a Reply