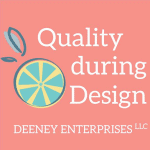
How Does Reliability Engineering Affect (Not Just Assess) Design?
Reliability Engineering isn’t just about assessments. It’s about providing information to make decisions. How does reliability engineering affect design?
We answer all the questions from the classical Kipling Method:
- What kind of design inputs can we expect from a Reliability Engineering working relationship?
- Why is their point of view important?
- When should we get them involved in the product development cycle?
- Who can we generally look to for a reliability engineering viewpoint?
- How can we get them involved?
- Where do we find out more information?
What’s today’s insight to action? Find out who the reliability engineers are in your workplace. They may not have the title “reliability engineer”. They may have a quality engineer title but be doing reliability engineering type of work.
Or they may be a design engineer with reliability engineering interests. If that describes you, then bookmark this website: QualityDuringDesign.com! There are lots of free resources and even some free training about how to use quality and reliability engineering methods during the design process. The information at QualityDuringDesign.com is geared toward product development engineers – it’s made just for you, so check it out!
I also send out a weekly email that is educational, inspirational, and fun. So, subscribe to the newsletter while you’re visiting.
Citations:
Related QDD episode:
5 Aspects of Good Reliability Goals and Requirements
Episode Transcript
We’re analyzing test results and want to evaluate the warranty of the products in our new product development project. So we make initial contact with our neighborhood reliability engineer, and they’re likely disappointed that we didn’t contact them earlier. When should we get reliability engineers involved and for what more after this brief introduction.
Hello, and welcome to Quality during Design the place to use quality thinking to create products others love for less. My name is Dianna. I’m a senior level quality professional and engineer with over 20 years of experience in manufacturing and design. Listen in and then join the conversation at qualityduringdesign.com.
When we develop a working relationship with a reliability engineer, as a member of the cross-functional part of the team, what we’ll get from them throughout new product development is information and data in the form of reliability planning, which then leads to assessments, test reports, and failure/root cause reporting – all data that can affect our design decisions.
So we want to involve them early.
I’m going to tell you a story, a metaphor.
We’re a bunch of friends out to a dinner except one friend. We totally forgot about her through ordering from the menu, eating salads. And through half of our main course, we call her as soon as we remember, and she comes rushing in it’s awkward, but we all make room at the table. She looks at our half eaten plates, still out of breath from trying to catch us at the restaurant before we left. “My uncle supplies this restaurant with their fish. He wouldn’t sell them any halibut because of some parasite that the local population has right now.” “Oh no”, we all think. Most of us ordered the halibut. She’s an honest sort of person and probably mentioned that to be helpful. If we had known about this halibut problem, we probably wouldn’t have ordered the halibut or maybe we would’ve asked the restaurant where they sourced their fish from. Our missing friend knew information that we didn’t, that would’ve affected our decision, but at this point we’ve already eaten it. What are the chances that the halibut the restaurant served us is infected? We get ill later that night and wonder why we didn’t invite our friend earlier.
Our group that’s out to dinner is our cross functional design team. And our missing friend is our friendly reliability engineer. Besides having the inside scoop on the latest fish monger information, reliability engineers can get involved in the concept phases of product development and then beyond.
One of the things that reliability engineers can help with during early concept design development is the reliability requirements, including what we define as a failure. Now, I had a previous episode of the quality during design podcast titled “5 aspects of good reliability goals and requirements”. Basically, these five aspects were a measurement of time, reliability at specific points in time, a desired confidence level, a definition of failure, and the operating and environmental conditions.
The definition of failure and where and how this product will be operating and in what environments are pretty critical to understand and reliability. And it’s also critical information for design engineers to know. Reliability engineers can help set up these reliability requirements so that they’re able to be verified in a test later. They can also help us assess if these expectations are realistic or even achievable. They consider things like how are we going to model the system? Is there a similarity to other designs that we have information on what’s the highest risk subsystems or components of this concept? And considering that existing baseline that we might know about: what’s new, are there new materials? Are there different parts? Is it being assembled a different way? Reliability engineers may get into if there is a design margin needed, a factor of safety.
Now defining the requirements and defining the failures and ensuring that the operating environmental conditions are defined – those are early project work that can be done at the concept phase. If we get further into development, reliability, engineers can also review the design specifications. They can look at the manufacturing production process and even supplier issues, looking at root causes and mistake proofing things. And they can conduct early reliability tests and environmental tests, which are done before the design is finalized and production ready.
After all of that, we’re back to where we started with this episode. We’ve got test results. Reliability engineers can help with the data analysis and root cause analysis of a failure scene during test.
How do we get reliability engineers involved? We just need to ask them or talk with our project manager about getting someone assigned or pulled in. At the very least, we need to be familiar with their value. So we’ll know when there’s a gap in our information because we want to perform risk based thinking – we want to know what risk there are. And a reliability engineer has a perspective about that.
What’s today’s insight to action? Find out who the reliability engineers are in your workplace. They may not have the title “reliability engineer”. They may have a quality engineer title, but be doing reliability engineering type of work.
Or they may be a design engineer with reliability engineering interests. If that describes you, then bookmark the website QualityDuringDesign.com. There are lots of free resources and even some free training about how to use quality and reliability engineering methods during the design process. The information at QualityDuringDesign.com is geared toward product development engineers. It’s made just for you, so check it out! I also send out a weekly email that is educational, inspirational and fun. So subscribe to the newsletter while you’re visiting the website.
If you like the content in this episode, visit quality during design.com, where you can subscribe to the weekly newsletter to keep in touch. This has been a production of Deeney Enterprises. Thanks for listening!
Leave a Reply