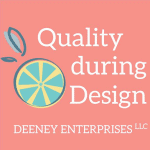
Gemba for Product Design Engineering
If you have quality friends, you may have heard of Gemba. What is Gemba and can it help with product design?
Gemba is an ideology.
And, yes, it can help with product design!
We explore how and talk about why you might want to adopt the term “Gemba” for product design engineering.
“Go to the actual place” where customers will be using your product, where it will be manufactured, and where it will be tested.
There are really two parts to the Gemba ideology:
- actively go to where it’s happening to observe and talk to others
take a partnership attitude with you when you do - For design engineers making decisions about components, specs, and tolerances, these downstream activities could be thought of as your internal customers.
Adopt the term “Gemba” or “Gemba Walk” to tag it in your memory as an ideology you can adopt when designing quality products others love, for less.
Citations:
Another resource about Gemba Walks:
www.leansixsigmadefinition.com/glossary/gemba/
Other QDD episodes that explore these ideas more:
How to Self-Advocate for More Customer Face Time (and why it’s important)
Product Design from a Marketing Viewpoint, with Laura Krick (A Chat with Cross Functional Experts)
The Who’s Who of your Quality Team
Internal Customers vs. External Customers
Episode Transcript
If you have quality friends, you may have heard of Gemba. What is Gemba? And can it help with product design? Gemba is an ideology and yes, it can help with product design more after this brief introduction.
Hello, and welcome to Quality during Design the place to use quality thinking to create products others love for less. My name is Dianna. I’m a senior level quality professional and engineer with over 20 years of experience in manufacturing and design. Listen in and then join the conversation at qualityduringdesign.com.
Gemba is a Japanese word with a literal translation that means, “the actual place”. Gemba is just one part of the Lean principles of quality. For a lean practitioner, Gemba embodies the idea that you need to actually go to the place where things are happening in order to identify areas for continuous improvement or problems that need to be solved for a manufacturing process. A lean practitioner may take a Gemba Walk, where they go to the place where the manufacturing process is, where the parts are being made. They talk to people. They talk to the manufacturing operators and they may talk to the inspectors. How’s it going? Are you having any problems? Are you experiencing difficulty doing this? And they also just observe how things are done, how parts are moved, how they’re assembled. And they look for those areas where they can make improvements.
Continuous improvement are those little tweaks and efforts that make things better a little bit at a time. And over time can have a big impact on lots of things: throughput, the bottom line operator happiness and so on. And like I mentioned, gemba is really part of lean. So it has its roots in manufacturing, but has expanded into other areas too, like hospitals for their systems and service areas (just as one example).
Gemba is surprisingly not listed in the quality management books I have on my bookshelf. I don’t know if that’s a reflection of me or maybe the books that I have on my shelf. Maybe it’s just assumed practice, but when you’re dealing with a thought implementation system, like Lean, it’s good to call out the people management aspect.
Giving a complex idea a name like Gemba is useful to help people remember to incorporate it in their daily activities and in their planning. It’s an important part of being part of a team, a manager, and a good leader. And it’s important, too, if you’re a design engineer, making choices that affect the downstream operations.
I did Gemba Walks before I even knew of the term. Call it curiosity or being nosy, if there was something going on with a project that I was involved with, I wanted to be there. They’re starting to make prototypes in the lab. Let’s go see what’s happening. Are they able to follow the procedures like we drafted them or are they making tweaks to the process to make things easier, better for them to make the product?
As a design engineer, you can also use the Gemba ideology for your own information and purposes. At some point, you’ve got a question about how a customer would do something with your new product. Would they hold it this way or use it for other purposes, arrange with your marketing or your commercial operations person, a visit with your customer and go to where the action is. Take a Gemba Walk with your customer, take your prototype or your drawings, or go to where they would use your product and see how they’re using other products. And look at their environment. Go to their actual place, ask questions, observe, and you learn a whole lot more than if you were just watching videos or making phone calls behind your desk.
Or maybe you’re specing out a new subsystem from a supplier. Your company already has relationship with. Maybe your company audits its suppliers, and maybe they have that supplier on their schedule. I don’t know if they would let you go with them, but it wouldn’t hurt to ask. Or you can talk with a supplier management person and ask about their experiences with other projects for this company. Maybe they can set up a meeting or a tour where you actually go to the place where your products are going to be made.
Or if you’re starting to write protocols for tests, for design V and V, and you’re thinking that you’re going to be doing a tensile test for something, go to the lab and talk to the lab technicians and the people that are operating the test equipment. Maybe take a part with you or a drawing of part. What are some of the problems that they could foresee with testing your product? Would it need to be held and fixtured in a certain way? Do they have those kind of fixtures or do you need to create something new, a new tool for them to be able to test your product? Or maybe they have an idea of a different way to test that would be easier for them and give you better results. Again, take a Gemba Walk to the test lab, to the actual place where it will be tested. Observe what’s there, how the part would be handled and talk to the people that would be handling it.
Actually going to the place where things are happening is one aspect of Gemba. The other is the attitude that we take toward the whole process. The other people that we’re talking to, the operators, the customers, the test technicians, they’re all partners in creating a quality product. As design engineers, we may take a Gemba walk into the test facility and into the manufacturing facility. And even though we are designing the tolerances and determining the specs, and what’s going to be inspected, the operators, the quality inspectors, the test technicians, they’re all are internal customers, and we can succeed better if we work together.
What’s today’s insight to action? Even though Gemba is an ideology, it’s a useful one and we can identify the ideology and keep it in mind by labeling it Gemba or Gemba Walk. It’s roots are in quality, but it has several uses for design engineering that could benefit your design and you!
Please go to my website at qualityduringdesign.com. You can visit me there. And it also has a catalog of resources, including all the podcasts and their transcripts. Use the subscribe forms to join the weekly newsletter, where I share more insights and links in your podcast app. Make sure you subscribe or follow quality during design to get all the episodes and get notified when new ones are posted. This has been a production of Deeney Enterprises. Thanks for listening!
Leave a Reply