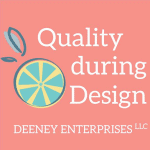
Use FMEA to Design for In-Process Testing
Our manufacturing friends are approaching us with a problem.
They want to test the product during manufacturing. The way the product is currently designed doesn’t let them do this, or not easily.
Can we make a design change so they can test?
Imagine that they’re coming to us with this question before we’ve completed the design. Can they really see the future?
Perhaps, with strategic use of FMEA. We talk through a scenario of how to do it.
What can you do today?
Work from your Design FMEA and identify components or functions that are critical. Communicate that with the manufacturing process engineering team and work with them on controls to mitigate risks during manufacturing.
Then, turn the tables: Ask the manufacturing process engineers what features of the design could help them with manufacturing. They’ll help you incorporate ideas so you can Design for Manufacturability.
Citations:
These other QDD episodes expand on some concepts:
Design Specs vs. Process Control, Capability, and SPC
Prevention Controls vs. Detection Controls
Use FMEA to Choose Critical Design Features
Episode Transcript
Our manufacturing friends are approaching us with a problem. They want to test the product during manufacturing so that they can ensure that it still functions after a certain process step, or that it’s still meeting minimum requirements. After they’ve done some processing and assembled components, the way the product is currently designed, doesn’t let them do this or not easily. Can we make a design change so they can test? Let’s talk more about this after the brief introduction.
Hello, and welcome to Quality during Design the place to use quality thinking to create products others love for less. My name is Dianna. I’m a senior level quality professional and engineer with over 20 years of experience in manufacturing and design. Listen in and then join the conversation at qualityduringdesign.com.
Our process engineering/manufacturing development friends want to change the design so that they can test it in-process. Meaning they’re in the middle of manufacturing and assembling components and they want to stop the assembly, perform a test to make sure that things are still right or correct, and then continue on with the manufacturing process to finish the product.
What are reasons that they’d want to test? Why would they want to do this? Well, one example is maybe the components are exposed to something above its limits. They could be concerned about a component getting damage during manufacturing, and that could be from lots of different things. It could be from electrostatic discharge, if you’re dealing with circuit components. Fumes from adhesive, corroding or building up a film on a component. Maybe a component is exposed to residual heat from a bonding process. Or maybe there’s some force from assembly that they’re concerned about damaging another component.
What kind of tests might they want to perform in-process, during the manufacturing proces? They may want a functionality test or a performance test. They might want to test something out electrically or perform a physical test. Or maybe there’s even some visual examinations that they want to do.
Imagine that they’re coming to us with this question before we’ve completed the design.
Can they really see the future? Well, maybe if we’ve got an experienced team, that’s looking at how things might happen. How would this be possible: to see into the future? Well, through strategic use of FMEA (failure mode and effects analysis).
We’re design engineers. So, if we’ve done a design FMEA, we’re going to have a list of potential failures that could occur and their causes. Let’s say part of our design includes a circuit board and one of the failures is functional failure because the board breaks. There could be several causes for the board breaking. Maybe it was exposed to electrostatic discharge, maybe the solder joint broke, or if there’s another failure.
The process engineers are figuring out how to make the product, including installing the circuit board component. They’ll be figuring out steps of assembly. They’ll start a manufacturing process FMEA and it’ll be following the steps of their assembly process. They’ll also look at the design FMEA (or they should). They’ll look at the design FMEA for the circuit board component and see that it could fail from ESD, a break in the solder joint,or another failure.
Now they’ll look at where their manufacturing process interfaces with the circuit board. Could something about their process introduce these causes and lead to a circuit board break? And they decide that the chances are pretty good: that, yes, there is something about their manufacturing process that could introduce these causes and cause a circuit board break.
Then they want to look into controls. They can add some prevention controls, like the ESD mats, or they can manage the forces at assembly. They decide they also want a detection control because this failure is associated with a high severity effect. So even if they do have preventive actions put in place, they still want to check it and be able to detect if there was still a problem.
If they can test the partially assembled product before they finish it, they’ll be able to better manage manufacturing. They can better do their qualifications. In all, it could be less reworks, less scrap and less issues in final testing…there would be a lot of benefits to adding a detection control.
Back to our “imagine this” scenario, where the manufacturing process engineers come to us with this ask before the design is completed. Could they really do this just by thinking about what could potentially happen by using FMEAs early in development?.We just did!
Now we, the design engineers, can look at how we can adjust or modify our design on paper to allow for an in-process manufacturing test that’s intended to catch problems with the circuit board before the product is finished being manufactured.
We’re adding detection controls for manufacturing during the design process, and we’re doing it early at a time when we still have wiggle room in the design itself – it’s less costly for us to make a change. We haven’t done verification tests, yet, verifying our design against its requirements. And the suppliers haven’t started customizing components either. So now is THE best time to be asked to change the design.
What’s today’s insight to action? We can do design FMEA at concept development. In addition to that, we can use design FMEA to communicate with the process engineering team. If we have a function or a component that is severe, likely to happen and/or difficult to detect, we can tell them. We point it out: We did our preliminary design FMEA. These components are critical. This is how it can fail. Can you note this as an important requirement for the manufacturing process?
And then we can turn the tables around. We’ve given them information. Now we can ask what we can do for them: Ask them if they think they’ll want to do in-process inspections or tests and what that might look like. How would they need the design to work to be able to do that? Now we’re asking our manufacturing process engineers for manufacturing requirements so we can better design for manufacturability.
FMEA provides us a way to capture our ideas and our expertise and knowledge and communicate it with other people on our teams. And it helps us to manage this data early in the concept phases when we’re still wondering, “What if?”
If you like the content in this episode, visit Quality during Design.com, where you can subscribe to the weekly newsletter to keep in touch. This has been a production of Deeney enterprises. Thanks for listening!
Leave a Reply