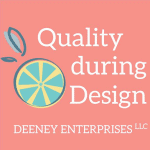
A Severity Scale based on Quality Dimensions
We can develop a severity rating scale based on us: our company, our customer, our product… And we can relate the categories that we use to the quality dimensions that matter to us.
We talk about the 7 principal quality dimensions of goods and services, the 5 principal dimensions of quality in customer service, and how we might customize our severity scale based on these dimensions.
CHECK ON IT: We need to be careful to comply with our own company’s policies and industry’s regulations. We may not be able to customize our severity scale because of these reasons.
The 7 principal Quality Dimensions of goods and services (Garvin):
- Aesthetics
- Features
- Performance (i.e. functionality of primary operating characteristics)
- Serviceability (able to be repaired)
- Durability
- Reliability
- Conformance
The 5 principal Quality Dimensions that contribute to customer perceptions of quality of a company’s services (Evans):
- Tangibles
- Empathy
- Responsiveness
- Reliability
- Assurance
We can create a severity scale that matter to us based on these Quality Dimensions, like the example, below.
When we’re defining our severity scale with our team, we need to make sure that we use it with intention during product development, including the concept phase. And that we understand how the scale was applied so that when we’re making decisions about our product’s design and our project, we’re making informed decisions.
Other episodes you might like:
5 Options to Manage Risks during Product Engineering
Remaking Risk-Based Decisions: Allowing Ourselves to Change our Minds
Citations:
Evans, James R. and William M. Lindsay. Managing for Quality and Performance Excellence, 11th ed. Cengage Learning, Inc., 2020, p.103-104.
Garvin, David A. “What Does Product Quality Really Mean?” Sloan Management Review, vol. 26, no. 1, 1984, p. 25-43.
Episode Transcript
We may be at the concept phase of our product development, and we’re starting to evaluate some characteristics and features of our concept ideas. We may want to start categorizing them. One of the ways we can do that is by evaluating the risk – specifically the severity: if this goes wrong, or if this feature is missing, how severe is it? How would we rate that with respect to the other things that we’re looking at?
We want to be able to get some priority over all of our ideas. What severity rating scale should you use? In this particular instance, we would want to look at both the customer’s perceptions and experiences and also the functionality of our product. There’s a way we can create a severity scale that is categorical and based on quality dimensions. There are seven principal quality dimensions of goods and services, and five principal quality dimensions that contribute to customer perceptions of quality of a company’s service. These are all the dimensions of quality that our product could have. Let’s get into this a little bit more after the brief introduction.
Hello, and welcome to Quality during Design, the place to use quality thinking to create products others love for less. My name is Dianna. I’m a senior level quality professional and engineer with over 20 years of experience in manufacturing and design. Listen in and then join the conversation at qualityduringdesign.com.
David Garvin suggested that products have multiple dimensions of quality and he listed seven principal quality dimensions of goods and services, and they go as follows: aesthetics, features, performance (or functionality of primary operating characteristics), serviceability (or the ability to also be repaired), durability, reliability, and conformance.
When we create a product, there’s the physical product itself, but it is also tied back to the customer’s perception of the product as it relates to the company. And that can be affected by all the interfaces that the customer has with the company. It could be on repairs and returns, customer service, shipping and handling, and all of the other interfaces that customers have with not just our product, but our company, too. Considering quality dimensions that contribute to customer perceptions of quality would also be a good thing to do when we are developing products. The five principals that relate to customer perceptions are tangibles, empathy, responsiveness, reliability, and assurance.
For a category goal severity scale – sometimes they are listed from zero to five or zero to ten: the higher the number, the more severe, the worse the situation is. It also may not be a number, it may just be a description of low, low/medium, medium, high, and so on. When you’re developing a severity rating scale with your team, with your cross functional team, you just want to make sure that it makes sense for your product. You also may need to comply with your company’s quality standards or policies and procedures or even regulations. So, check into that too, before you start making decisions with a severity scale,.
If we’re in the early concept phases, and we’re just trying to get an idea, we can create a severity scale that would be related to the quality dimensions that we just talked about for the descriptions of the different severity levels. We can relate the customers perceptions of quality with the product quality dimensions. For example, one of our quality dimensions of our goods and services is aesthetics. And one of the quality dimensions related to our customers is a tangible experience. We could group those into one severity category, so it could read like this for the product: “The product is fully functional, but has a defect. And the aesthetics is negatively affected.” That would be the quality dimension of our product itself. On the customer side: “The customer can use the product as is with a defect, but notices it, and their tangible experience of the product is negatively affected.” Tangible experience is a quality dimension of our customer’s perception of quality. I’ll post an example of a severity rating scale that correlates customer experience and product functionality. And those categories include these quality dimensions that we’re talking about. It’ll be located on the blog for this podcast.
Something else to consider with the severity scale and its descriptors and categories is just your company’s mission and vision in general. Are you working for a company that is passionate about environmental safety? Then maybe you will want to add a column about environmental safety of your product. Are you working in an industry where it’s really important that a procedure get finished with the product that you’re using, then maybe you would want to add a column that relates to the procedure that your product is involved in and independent of the quality dimension of your product. You can customize the severity level descriptors for your product, for your company and for your particular customers.
If you use a severity scale like this, you just need to be consistent with it. Defining a severity scale is something that the team should do together before any analyses are done. If we think of risk analysis like performing a test, having the severity scale and some acceptance criteria is like having a test protocol in hand before you run the test.
The severity scale we’re talking about is for concept development. You may want to iterate on the work that you’re doing during concept development into the later steps of the product development process. You may want to consider relating your severity scale with the rating scale that you will use in other risk analyses (like FMEA) for your project.
What’s today’s insight to action? There are a lot of standard, published rating scales for severity out there and available. You’re not stuck using them. You can customize a severity scale to fit you, your company, your product, your customers… You can use categories based off of quality dimensions, like we talked about today. As long as when you’re defining your own severity scale, that you’re using it with intention during product development, including the concept phase. And that you understand how the scale was applied so that when you’re making decisions about your product and your project, you’re making informed ones.
If you like the content of this episode, visit quality during design.com, where you can subscribe to the weekly newsletter to keep in touch. This has been a production of Deeney Enterprises. Thanks for listening!
Leave a Reply