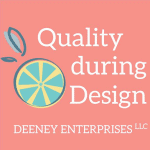
Why Yield Quality in the Front-End of Product Development
During the product development process, are there so many design prototypes but the team’s still not getting buy-in?
Are design concepts changing mid-development after it’s “too late” to change the design?
Are designs picked-apart only after they’re nearly done?
Late in development, are there many fires to fight with too many surprises at test?
Quality during Design is not about compliance activities. It’s about being proactive with our team in early development. And knowing how to have conversations that gets us what we need so we can engineer designs.
We explore why Quality can help us PRUNE the development process just by the nature of how it’s used.
And we highlight the 3 areas that we focus on in Quality during Design: risk-based decisions, quality and reliability engineering partnership, and the user’s process.
We can find Quality at the back-end of product creation, where it’s used for compliance.
We want to pick up some of it and move it to the front-end, where design decisions are happening.
It’s there that we can yield like a tool to work with our cross-functional team, to help us doing the engineering work that’s important for great designs.
Citations:
More about the Quality during Design Journey
Other Quality during Design podcast episodes you might like:
Quality as a Strategic Asset vs. Quality as a Control
More about the PRUNE strategy:
Quality during Design Framework: PRUNE – Quality During Design
The driving forces behind Quality during Design:
First time here? – Quality During Design
Other podcasts on Accendo Reliability and reliability.fm.
Reliability.fm The Reliability Engineering Podcast Network (accendoreliability.com)
Episode Transcript
During the product development process, are there so many design prototypes, but the team still not getting buy-in? Are design concepts changing mid development after it’s too late to change the design or are designs picked apart only after they’re nearly done later in development? Are there many fires to fight with? Too many surprises at test. This can be the experience we have with new product development processes and projects. Now, Quality during Design is about empowering product design engineers with methods to use to avoid these kind of problems. Quality during design is not about compliance activities. It’s about being proactive with our team in early development and knowing how to have conversations that gets us what we need so we can engineer designs. There are three areas we focus on and everything we offer at Quality during Design, including this podcast. Let’s talk more about that after this brief introduction.
Hello and welcome to Quality During Design, the place to use quality Thinking to create products, others love for less. Each week we talk about ways to use Quality during Design, engineering, and product development. My name is Dianna Deeney. I’m a senior level quality professional and engineer with over 20 years of experience in manufacturing and design. Listen in and then join us. Visit Quality during Design.com.
Do you know what 12 things you should have before a design concept makes it to the engineering drawing board where you’re setting specifications. I’ve got a free checklist for you and you can do some assessments of your own. Where do you stack up with the checklist? You can log into a learning portal to access the checklist and an introduction to more information about how to get those 12 things. To get this free information, just sign up@qualityduringdesign.com. On the homepage, there’s a link in the middle of the page. Just click it and say, I want it.
I’m dedicated to placing quality in more hands to be used earlier in decision making because I’ve seen it, I’ve seen how it works. I use these methods with teams I’ve worked with and I coached other engineers on how to do it and what to look for and how to apply it so that they can have the information that they need to make good design decisions. When we apply quality to the design, engineering and design development process, I like to think of it as we’re pruning the development process as it grows, as we’re doing the development and learning more about a project and the letters of prune stand for something, it’s an acronym. A lot of the tools and methods that we teach at Quality during design have these kind of principles.
P: They are people focused. A lot of the tools are focused on getting a team together to talk and discuss options, to explore ideas. A lot of them are meant to graphically or visually represent that for better communication, quality and reliability. Tools are also people focused and that their customer centric, they put the use and the safety at the center of the analysis.
R in our prune acronym is risk based. We can make design decisions based off of risk in really early concept development. We don’t need to have a finished design to start analyzing risk and prioritizing decisions off of that. We can just have a high level concept and a vague idea of how things might work. When we look at risk and risk concepts early, it’s going to help us figure out the design, how it’s supposed to look, what components and subsystems would be best to meet the needs of our customers. Then we can take that and iterate on it throughout the development process, getting more detailed as we need to so we can address risk-based problems and design for all the internal customers.
The U in our prune acronym is that these methods help us uncover ideas early, brings teammates together toward a common goal if only for a meeting.
N stands for Navigate Decisions because we’re working with our team, we’re looking at information. We’re able to facilitate navigating the team through a decision process or get the information that we need so we can navigate decisions with data.
And E means that it empowers the whole team to be a participant in the design engineering process.
If you followed this podcast for a while, you might have noticed that there are three major areas that we focus on in Quality during Design.
One is risk. We look at ways to analyze risk, including FMEA, and we look at ways that we can use those risk analyses to inform our decisions and how to use them with a team.
We explore quality engineering ideas, looking at our internal customers and how we can address or at least acknowledge that there’s variation in everything, including manufacturing, test and measurement, and understanding how that affects design decisions like tolerancing. And reliability engineering (I group that with quality engineering): we use reliability engineering to learn more about our choices and options in early phases of development and before verification and validation.
And the third area that we focus on is really the users. When our users take our product and use it, they go through a process, so we borrow ideas from manufacturing and project management to look at the user’s process to learn about it, to learn about who all the users are, where mistakes might happen, and how to design for the user in general.
Everything that we produce under Quality during Design falls into these three kinds of categories and it is these three areas that we focus on in the Quality during Design Journey. The Quality during Design Journey is our signature course designed for product design engineers and anyone involved in new product development. The Quality during Design Journey is a three-part course focused on those three areas. It’s online and asynchronous, but it has coaching elements too.
This is Thanksgiving week, where I am in the United States, and it’s really my favorite holiday because (at least with my family) it’s just about giving thanks, pausing, and giving recognition for the things that we should be thankful for.
With Quality during Design, I’m thankful that I’m able to share my knowledge and expertise with others to help make product design development better, to make it easier to talk with cross-functional teams and get that information and early development.
I’m thankful that you are listening! We’re really close to having 4,000 podcast downloads. I also appreciate that we’re being syndicated on Accendo Reliability, joining with their family of podcasts.
And I’m thankful to you. You email me when you’re inspired by a topic. You answer my questions and continue the dialogue. You add comments to the blog post to share with others.
And you share it! You tell me stories about, “I heard this episode, and I forwarded it to my colleague.”
And, if you’re subscribed to the newsletter (which if you’re not, get on that! Why aren’t you?), you’ve been hearing from me weekly with a little extra inspiration and information.
What’s today’s insight to action? Let’s move quality. Right now, it might be the end of the product development process where it’s only used for compliance activities to check that things were made right or made to requirements or specs. Let’s pick it up and move it to the beginning of the product development process. We can yield it like a tool for us to work with our cross-functional team to help us do the engineering work that’s important for great designs.
If you like this topic or the content in this episode, there’s much more on our website, including information about how to join our signature coaching program. The Quality during Design journey consistency is important, so subscribe to the weekly newsletter. This has been a production of Deeney Enterprises. Thanks for listening!
Leave a Reply