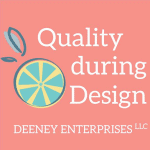
Journey from Production to Consumption: Enhancing Product Reliability
When you design a product, you consider the field reliability. Use environment usually comes to mind first. Do you also consider the stresses it undergoes from its creation to the end user’s hands?
We talk about designing for reliability, accounting for not just the product’s use but also its journey from production to the consumer. As a part of our in-depth discussion, we’ll look into the role of various environments – field and production – in affecting a product’s reliability.
By the end of this episode, you’ll see field reliability as including the various stresses acting on a product from its inception. So, buckle up as we embark on this journey to rethink reliability during design.
We’re not just designing a product to meet the needs of an end user, including meeting a certain reliability goal and use.
We’re also designing a product that can be made with a certain reliability.
Consider what’s happening to the reliability of the product through manufacturing, production, test and inspection processes, shipping and handling and the various use environments. Talk with the cross-functional team early so you can start to develop those design inputs.
Other Quality during Design podcast episodes you might like:
What is Production Equivalent; and Why Does it Matter?
Internal Customers vs. External Customers
Other podcast episodes you might like:
SOR 812 Storage of Test Parts – Accendo Reliability
Episode Transcript
So we think we’ve designed in reliability into the product. When does the reliability clock start ticking? When does our product start to degrade or when do stresses start affecting our product? As soon as the first component is made. We design for field use. Let’s look more at when the field actually starts. After this brief introduction.
Hello and welcome to Quality During Design, the place to use quality thinking to create products others love for less. Each week, we talk about ways to use quality during design, engineering and product development. I’m Dianna Deeney. I’m a senior level quality professional and engineer with over 20 years of experience in manufacturing and design. Listen in and then join us. Visit qualityduringdesigncom.
When you’re designing a product and someone mentions the field environment, what is the first thing you think of? The first thing I think of is the use environment. At this point, our product is done, it’s a reality and it’s in the hands of the customer. And when I think of field environment, what comes to mind for me is that our users are in a remote corner of the world and depending on this product, this thing that we’ve made to work, to work for them. It might be extreme conditions, like maybe they are out at sea or in the middle of a desert or not. Maybe it’s a home appliance and it might be abused every day with rough handling. No matter what the things we design are going out into the world or into space and being used by someone, even if it’s built into an automatic system, someone is buying and installing this system and depending on it to perform a function in whatever environment they’ve placed it in. These are all things we need to figure out when we’re designing for reliability.
We might need to do some research and perform some studies to better understand this use environment and how it might be used. We may rely on some standards from our own industry or a different industry to help us define the limits of this environment. And we also visit our customers and the place they want to use this potential device and talk with them about the field. We designed for the field.
The parts that we design or that we’re designing with – they’re made. As soon as they’re made, they’re seeing stresses. They’re handled, they’re manipulated during production, they’re assembled to other things or they’re fit into places. People or machines grab, twist and push these components into other components or parts. Just in the manner of being handled, they’re dropped and shaken or exposed to chemicals like bloom from adhesives that are being used somewhere else, or heptane washes or even oils on an operator’s hands. They could also be exposed to electrical charges. So we’re not just talking about physical handling, but exposure to other things static electricity and sparks from test equipment. These components, as they’re being made, they’re also being shipped around between workstations in a facility, between manufacturing facilities or manufacturing plants, over oceans, in airplanes and boats. Finally, they’re also stored. They’re stored in warehouses and holding places, on shelves for distribution.
Now I had a salesperson complain that their sample product that they were taking around to customers to get some initial feedback on it broke when they went to show it to the potential customers, and that was really embarrassing and they were upset about it. Rrightly so. Then I learned that they served customers in Arizona. It was summer and they were storing the product in the trunk of their car. Talk about extreme storage conditions!
By the time our product is assembled and placed into the hands of our end users, the parts have already seen a lot of stresses. So then the bigger question is: did we design for reliability considering how our product will be made? Did we consider all the stresses that these parts could see from when it’s starting to be made through to the user’s hands.
I mean, yes, we have production controls. Quality control measures work to minimize variation and reliability testing might be part of the production process, like burn-in to reduce infant mortality or stress screening to remove defective parts that would affect reliability. There is a lot that manufacturing, production and quality can do that affects the final reliability of the product, but there are limits and some controls add to the cost to make the product. We know when we’re testing our product we want to test it in its production equivalent state so that these stresses are built into the product that we’re testing. We talked about production equivalence in another episode and I’ll link to it in the podcast blog.
Even with these production controls and understanding how we’re going to be testing our product, we can still design for reliability, considering the production environment as part of the field environment or as an additional environment that our product needs to survive. Imagine how much easier and successful the product reliability could be if we not only design to the end user environment but also to the production environment, design for reliability for the whole of the product.
Where are we supposed to get that information? We get that kind of information from our cross-functional team: the process engineers, the manufacturing, production people, quality engineers, reliability engineers. They will have input into the product and how it’s designed. They’ll likely know the handling that will be needed, the storage capabilities that we have and other production effects that may affect the overall reliability of a product. Actually, it might be easier to get that information than it is to get clarity and alignment on the use environment. After all, we’re not just designing a product to meet the needs of an end user, including meeting a certain reliability goal and use. We’re also designing a product that can be made with a certain reliability.
What can we do about what we’ve been talking about today? Consider what’s happening to the reliability of the product through manufacturing, production, test and inspection processes, shipping and handling and the various use environments. Talk with the cross-functional team early so you can start to develop those design inputs. Visit qualityduringdesign.com and subscribe to the newsletter. The website also has a podcast blog, which is the episode of this podcast with extra show notes and links. For this particular episode. I will link to other quality during design podcast episodes that relate to this idea. This has been a production of Deeney Enterprises. Thanks for listening.
Leave a Reply