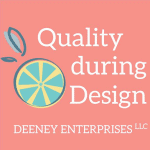
Driving Effective Conversations-Three Major Aspects to Consider for DfX
Gain insights into working effectively with cross-functional teams, collecting invaluable design inputs without succumbing to the overwhelming flow of information.
We’ll discuss the magic behind the ‘concept space’, an efficient approach to dissect potential customer experiences, streamlining concept development at the start.
What about after that high-level concept development, when we begin our engineering design?
Early engineering diagrams can prove instrumental in evaluating modularity, layout, and interactions in product design with a team. Dianna guides us through part of a Quality During Design course lesson, shedding light on how these diagrams can be used. Each function has a different reason to look at these three aspects of product design, and it’s worth asking to help us achieve Design for Excellence.
Learn how the collective wisdom of these teams can influence design choices, ensuring that the final product appeases both the internal and external customers. So, buckle up for this enlightening episode as we demystify product design and stress the crucial role of a synchronized team effort.
Product design is an intricate, complex process that demands effective collaboration. Engineering concept diagrams can help in evaluating modularity, layout, and interactions in product design. These diagrams help visualize the different components and interactions of a product design. Collective inputs from teams can significantly influence these design choices. It ensures that the final product appeals to both internal and external customers, leading to a more successful product in the market.
This episode demonstrates that successful product design is not just about the individual designer’s creativity but also about effective teamwork and the collective wisdom of the team. It shows that a synchronized team effort is crucial in navigating the complex web of product design.
Whether you are a product designer, a quality professional, or anyone interested in the field of product design, the insights and strategies shared in this podcast episode can significantly enhance your understanding and practice of product design. It’s a journey through concept and collaboration, unraveling the intricacies of product design, and highlighting the power of teamwork in navigating product design.
Other Quality during Design podcast interviews you might like:
Foundations-Understanding Cross-Functional Collaboration
Driving Effective Conversations-Taking the Lead in Working Meetings
Video background designed by Freepik.com
Episode Transcript
Welcome back to the Quality During Design podcast. I’m Dianna Deeney. Product designers have a lot of customers, internal and external. What are ways to approach concept development that helps us work with our cross-functional team and get design inputs without getting overwhelmed and without it taking forever? Listen in after this brief introduction.
Hello and welcome to Quality During Design, the place to use quality thinking to create products others love for and less. Each week, we talk about ways to use quality during design and product development. I’m your host, Dianna Deeney. I’m a senior level quality professional and engineer with over 20 years of experience in manufacturing and design. I consult with businesses and coach individuals on how to apply quality during design to their processes. Listen in and then join us. Visit qualityduringdesign.com.
We’ve been talking about staying in the problem space longer for concept development, working with our cross-functional team to develop design inputs the information that we’ll use to actually design against. There are many ways to design for external customers. Quality during design uses a concept space to help you focus on one customer aspect at a time. When things go right with our product, what are the benefits that our customers see and experience? When things don’t go right, what are the symptoms that our customers experience and when they’re using our product, what’s it like? Where are the hangups? Where could mistakes be made? What are ways that we can streamline and make things better Within this concept space? We’re using ideas like benefits, symptoms and the potential use process to evaluate a concept, an idea. We haven’t started engineering design yet. We are really working with some of the what-ifs, but also some of the targets the things that we want to go for, the competitive advantages that we want to target, the things that we’ve noticed about our old versions of products that don’t work out so well, the things that our cross-functional team sees or understands from existing customers or from our new customer base that affect the way that we design the product. Designing to a concept space with our cross-functional teams helps us to develop those design inputs early in concept development.
Those are some of the first steps that we can take with our cross-functional team to develop those design inputs. We don’t just leave those ideas or those concepts at concept development. We take what we’ve learned and we iterate on them throughout the product development process. In this way, we’re able to continue the conversation with our cross-functional team and we’re able to continue to get decisions based off of good information that early, fact-based concept development will help us throughout product development and we’ll be able to evaluate things based on our customers’ experience and the priorities that we want to target for those.
Once we start designing, to really design for excellence, we need to continue to check in with our team specifically about our designs, modularity, layout and the interactions that it has with itself, with the different modules and also with the external environment. I’m going to share with you a little bit of one of the Quality During Design courses. This course talks about using specific types of diagrams, specifically a schematic, a geometric layout and an incidental interactions diagram to look at these three aspects of any new product design its modularity, its layout and its interactions. Engineers will create these kind of diagrams. The idea is to review them with our cross-functional team.
The part of this course that I wanna share with you today is what kind of input or what kind of effect the cross-functional team’s opinions might have on these three things, these three aspects of our new product design. By understanding why we might want to change our design depending on our cross-functional viewpoints and their input, we’ll gain a better understanding of what kind of questions to ask and what kind of open-minded learning we want to maintain when we’re working with our cross-functional team on our new product design. Let’s get into sharing part of that lesson.
What kind of design choices are we really making from these diagrams? These diagrams really explore three aspects. It’s exploring the modularity of a design. It’s layout of components and parts and the interactions that we have with them. Interactions are coming from our schematic the first drawing that we create and the incidental interactions are the things we’re considering after a geometric layout. With those two diagrams, we’re considering both the fundamental interactions and the incidental interactions.
Why is it so important for us to use these diagrams to develop engineering designs at a concept phase early? Because it takes a team to deliver a product. Our goal is to guide them through working meetings to get their input into the design itself. We’re using these three concept development tools to talk more about specific parts of the product’s features and characteristics, but doing it in a way that lets us explore design choices before we go too far down the path of engineering solutions. Sometimes that learning is an aha moment. Other times it will bring up more questions. It’s our responsibility to ask, because they are the internal customers of our design choices or they represent our end users, which are our external customers. They are going to be giving us input into the product design, what needs to happen for the customers and to be able to make this be made with a certain level of quality.
When we create these three diagrams and look at these three areas modularity, layout and interactions and we work with our team, we can think of each of our teammates and think of what each can provide us in terms of design inputs.
First, let’s start with our customer-facing teammates. This could be sales and marketing, customer service field operations anyone that has an understanding of the customer themselves and also where it is they are working in the use environment. With modularity, something they may come to the table with or have thoughts about is product variety. Are you designing and developing something where the customers are expecting to be able to upgrade or to have a different level of product, like a bronze, silver and a gold, where they can upgrade different modules of the product design in order to get different benefits from it? Modularity could also affect the interchangeability of things too, if you think of disposables and service, repairs and other upgrades. What kind of capabilities do we want to offer the customers there? Our customer-facing teammates may have some strong opinions about that. Regarding the layout of this design concept, they come to the table knowing a bit about the competitive products. How do the competitive products meet the customer needs? That might affect what users expect to be able to do, and is there an existing difference between what they currently do and what they really wish they could do? Our customer-facing teammates may also look at layout and think about the interfaces of our user human and maybe other products within the use space and as far as interactions, they may be very familiar with the use environment, with the extremes that this product is going to be working in, or with service and handling and delivery. They want to be able to deliver it easily, not need a refrigerated truck, for example. These are some of the perspectives that our customer-facing teammates may have about this new product design and definitely design inputs that we want to be able to capture and design against.
Let’s next look at reliability. They do a lot of tests to learn and they verify that the product is reliable. With our schematic and its modularity, they’ll be thinking about what are the risks, what’s new, what’s different and what’s unknown. What are the reliability goals for the whole system and are there particular modules that need to be more reliable than others and what are trade-offs? Reliability engineers may help with redundancy and apportionment, which are things that are affected by the modularity With interactions. Reliability engineers are going to be looking at the use environments. They’ll want to be able to plan reliability analyses and testing that may affect the modularity and layout of the product.
Next, let’s talk about our cross-functional teammates involved with production. This is manufacturing and procurement. They’re working with suppliers. They’re making sure that the product can be made. Our production teammates are thinking about design for manufacturing how might it be manufactured in modules and what manufacturing processes would be needed. They also think about the capability of this being able to be produced. What tolerances would be needed, what kind of resources would be needed and do we have them or do we not have them? Would we need to outsource them and what risk would that introduce? And they also look at costs. Even with the incidental interactions, they’re going to be looking at what’s new and different and unknown and seeing if there’s any special handling and storage requirements or maybe even manufacturing environmental needs. An example of that would be clean rooms for cleanliness, rf shielding for electronic assemblies.
Our quality teammates are going to be looking at our new product design concept with respect to quality, processes and transfers, controlling variation and controlling risks, and they bring knowledge about production benchmarks and capabilities. Some quality teammates take a very broad approach to product development and they’re looking at the transfers of information and parts between development and production and the business. They’re interested in learning what the overall quality goals for this new product are and about how we’re going to meet them. Things like what quality measure is defined by a module, where are natural breakpoints to assess the quality of the product, where might we have new suppliers and where might we be stretching the limits of our current suppliers, where our user interface is with this system and what quality measures are the users themselves defining. They may also be thinking about how to design with testing in mind, either in process testing or final testing, or even testing that happens in the field after release. These are a few of the things that the quality person on your cross-functional team might be thinking about with new product development.
And finally, project management. Someone has to coordinate everybody to get the project done. They bring knowledge about the development capabilities what are the resources and the costs and the timelines and those are usually constrained. The product design modularity may affect project management. Maybe different teams need to be working on different modules in order to meet the market need in the time the company needs to meet it. Project management decisions are also affected by the product layout and the interactions of the product.
And finally, we share and then we iterate these diagrams for design, for excellence.
I hope this episode today gave you a different appreciation for the kind of values your cross-functional team might have toward your product design decisions.
If you want to learn more about these three different kind of diagrams and how to work with your team on them or with any of the other quality and reliability tools we talk about in early concept development, contact me at QualityDuringDesigncom. This has been a production of Deeney Enterprises. Thanks for listening.
Leave a Reply