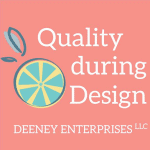
A big failure and too many causes? Try this analysis.
We have identified a failure of our design. It’s a complicated failure that has multiple potential root causes, and some that are conditional. Is there a tool that can capture it all and help us prioritize our reactions to get rid of this problem? Yes, there is: Fault Tree Analysis!
Learn what it is and how it can help us get a handle on that big failure:
- all of our causes are mapped out in a visual diagram
- we can identify cut sets
- we can see where to prioritize resources where its best to eliminate or reduce causes
Once you’ve had a chance to listen, I want to hear from you. Share your answers to one of these questions in the comments section.
How many times has your organization used FTA? Does your organization reserve it for the worst cases, or is it routinely performed?
Citations
Episode Transcript
You have identified a potential failure in your design, and it’s a complicated one. It has multiple potential root causes. Is there a tool that can capture it all and help prioritize your reactions to get rid of this problem? Yes, there is, and its fault tree analysis. Stay tuned after this brief introduction.
Hello and welcome to quality during design the place to use quality thinking to create products, others love for less. My name is Dianna. I’m a senior level quality professional and engineer with over 20 years of experience in manufacturing design and quality. Listen in and then join the conversation at qualityduringdesign.com.
You have identified a potential failure in your design. The best-case scenario is that you’ve discovered this early in your design phase, either through an analysis or some benchtop testing. Worse, you discovered it during verification testing. Or, at the worst, you’ve discovered field failures. This failure mode is a complicated failure. It has multiple potential root causes. There is a tool that can help you breakdown this failure into something manageable that you can take action against, and this tool is a fault tree analysis (or FTA).
A fault tree analysis breaks failure events into specific causes and combinations of causes. It can identify changes you can make to reduce the chance of a failure event from happening or even eliminate the failure from happening altogether. Fault Tree Analysis is a narrow process. It analyzes one failure at a time. If you’re concerned with this one big failure that’s happening and you want to get it fixed, fault tree analysis might be the right tool for you.
Visually, a fault tree analysis is a tree diagram, except it’s turned on his head and inverted. The trunk of the tree is the failure mode, and it is at the top of the analysis. Coming down from the failure mode are several branches that have causes, and each level of cause is another cause for the one before it. It’s a tree effect, where we drill down through our causes to get the root cause, or to a place where we can take action and reduce or eliminate this failure.
Fault tree analysis is not just a list. It is a drawn diagram of causes, and it associates conditional events. Conditional events are when two or more things need to happen at the same time or sequentially for another event to happen. For example, your product is in a certain setting state and then the user happens to twist or orient it in just the right way. If those two things happen at the same time, it could lead to a failure. That’s a conditional event, and it’s very easy to see these on a fault tree analysis diagram.
Another useful thing about fault tree analysis is that it can capture the probability of failure for each cause that’s in your diagram. A quality or reliability engineer may be able to take that information and calculate probabilities elsewhere in the analysis. For example, what is the probability that this failure will be caused by these series of causes?
How does fault tree analysis help with a big failure?
- First of all, it identifies cut sets. A cut set are basic events that caused the top event to happen. If you eliminate or reduce the likelihood of a basic cause from happening, you reduce the chance of that failure.
- You have all of your causes mapped out in front of you in a visual diagram, which by itself is very helpful.
- If you know (or can estimate), the probabilities of each of those causes, you can travel up a chain of events and calculate what is the likelihood that these chain of events caused this particular failure. If you have a failure with lots of causes, it can be useful to identify which cause you should focus your resources on to get rid of. Maybe you have a failure mode and there are three major causes for it. If one of those major causes creates the fault 85% of the time, then focus your resources on solving that cause.
Now, what can you do with what we’ve been talking about today? When you have a single fault that you’re trying to solve that’s complicated, consisting of many different causes or dependent combination of causes, ask your reliability engineering professional to facilitate a fault tree analysis with your team. This will help you discover the root causes to take action to address.
I’d like to hear from you. How many times has your organization used fault tree analysis? Do you reserve it for the worst cases, or is it routinely performed? Please visit quality during design.com to this blog podcast and add your comments. This has been a production of Deeney Enterprises. Thanks for listening.
Leave a Reply