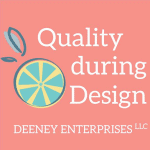
Remaking Risk-Based Decisions: Allowing Ourselves to Change our Minds.
Recent news highlights an accident involving a product with tragic results. This podcast explores this as cautionary tale and example outside of our own design house. The goal is to shift our perspectives to let us gain a better understanding of risk-based decisions.
We also talk about allowing ourselves room to change our minds about risk acceptability when we learn new information, both during the design process and from the field.
I’ll be following this story to see what happens. I suspect it may be years until it’s fully resolved.
What do we do with this information today?
- We can recognize that use environment and user process is a really important input into the design process, not just for dependability and user experience but also for safety.
- Remember that people make decisions on if a product’s design is ready to sell to consumers. Risk analysis can help us evaluate the information so we can make the best decision possible.
- We need to allow ourselves room to change our minds about the acceptability of a product given new information. Sometimes that’s having a contingency plan.
Once you’ve had a chance to listen, I want to hear from you. You can comment on this podcast blog. What is one consumer product that you use that has built-in safety features as part of the design that you appreciate?
If you like this podcast or have a suggestion for an upcoming episode, let me know. And share this podcast with your designing peers.
Citations
If you want to read the press releases and articles we talked about in this podcast, they’re cited here:
“CPSC Warns Consumers: Stop Using the Peloton Tread+.” United States Consumer Product Safety Commission, release no. 21-113, 17 Apr 2021. www.cpsc.gov/Newsroom/News-Releases/2021/CPSC-Warns-Consumers-Stop-Using-the-Peloton-Tread.
“Peloton Refutes Consumer Product Safety Commission Claims, CPSC Publishes Misleading, Inaccurate Bulletin on Tread+ Product Safety.” PRNewswire, 17 April 2021. PRNewswire. https://www.prnewswire.com/news-releases/peloton-refutes-consumer-product-safety-commission-claims-301270942.html
Pisani, Joseph. “After child dies, US regulator warns about Peloton treadmill.” AP News, Associated Press, 17 Apr 2021. https://apnews.com/article/product-safety-be5516665f9a2c7c4bb9b9441d4aef01
UPDATES since this podcast aired
May 2021 Recall Notice from the US Consumer Product Safety Commission: Peloton Recalls Tread+ Treadmills After One Child Died and More than 70 Incidents Reported | CPSC.gov
Nov. 2021 podcast interview with Peloton CEO: Safian, Bob, host. “Rapid Response: How Peloton keeps pushing through resistance, w/CEO John Foley.” Masters of Scale: Rapid Response, WaitWhat, 4 November 2021, http://listen.mastersofscale.com/JohnFoleyRREP?c=t0xm42zUlTZUIpO7MQdbfQ&h=866f4084497379d46
Episode Transcript
There’s some news that came out over the weekend that was very sad and tragic. It involved a product that was released to market and the field information is showing that people are getting injured, and there has been a death. So, this is a case of our product is in the market and we’re hearing of disastrous news where our product could be involved in tragic accidents. We need to remember to allow ourselves room to change our minds about the acceptability of a product given this new information. And that’s throughout the design process and after it’s in the field. Sometimes, that room for change is from having contingency plans. In this podcast, I’ll be examining that recent, real-world event that’s still developing. We’ll talk about risk analysis and risk-based decisions after this brief introduction.
Hello and welcome to Quality During Design, the place to use quality thinking to create products, others love for less. My name is Dianna. I’m a senior level quality professional and engineer with over 20 years of experience in manufacturing, design, and quality. Listen in, and then join the conversation at qualityduringdesign.com.
I mentioned that there was a big news story over the weekend of a product safety issue. This is a new story, so it’s still being told. I’ll be following it to see how it resolves, and you may want to, also. But I want to talk with you about it because, as someone involved in quality and reliability and product design (and as a consumer and parent myself), the story is a little scary. For us, in the design world, it can at least be a cautionary tale. So, what I want to do today is to evaluate from the outside what may have gone wrong. And why do this exercise? Because it provides an example outside of our own designs which can shift our perspectives and let us gain a different understanding of risk-based decisions. Maybe we’ll become better designers for it.
Here’s the story: It involves a high-end treadmill manufacturer that’s market to in-home, residential use. Its main feature is that it’s connected virtually to a community of trainers and other people using the same equipment for fitness. The news happened on Saturday and it started with a press release from the United States Consumer Product Safety Commission. They reported 39 incidents of things children and pets being pulled, pinned, and entrapped under the rear roller of the treadmill. They later clarified that it was at least one pet. Twenty-three children were involved in these incidents and the injuries from these events led to fractures, scrapes, and the death of one child. They were urging people that have this treadmill to stop using it if there are small children or pets at home. Or use it only in a locked room. The press release also had a video attached which was from the perspective of a nanny cam. The treadmill manufacturer then issued a news release in response (same day). They said that the warning from the Safety Commission was inaccurate and misleading, and the company said, “There is no reason to stop using the treadmill as long as all warnings and safety instructions are followed.”
Now, I’ve posted both press releases on this podcast blog at quality during design.com so you can go there and check it out if you’d like. And I want to note that I’m not associated with either the Consumer Product Safety Commission or the treadmill manufacturer, so I don’t have the inside scoop.
Let’s start to evaluate this from a design perspective, just with what we know from the press releases. The product involved is a treadmill marketed for residential in-home use. These aren’t the kind of things that are sold at local gymnasiums. There is an ASTM International “Standard Specification for Motorized Treadmills”, but I didn’t see anything related to this particular type of event in its abstract. We know that there’s field data of bad things happening. Children and pets are getting pulled under the rear roller. Based on the information from the press releases and the video that I watched, I would say this is not a product malfunction or a break. I also don’t think this is a case of misuse. Misuse is improper use of a device or someone is using a product to do something for which that product was not intended or designed to do. The example of misuse that I always think about first is a push lawnmower used to trim a hedge. The push lawn mower is a motorized lawnmower. You move it forward along the ground by pushing a handle and you walk behind it. The misuse happens when somebody grabs it by its bottom (or blade box) and swings it vertically to trim a hedge. This has happened. The uses of this treadmill aren’t like that. I also don’t think it’s misuse because it is being used inside the environment for which its marketed and as exercise equipment. There was at least one incident reported to have happened while an adult was using it. For those reasons, I don’t think it’s a product malfunction or break and I don’t think its misuse. I think these are accidents associated with the product.
From a design perspective, what could have gone wrong during the design process or what could have been done differently? Now, just remember, we’re doing this exercise to maybe learn something to think about our typical work from a different point of view, all to become better designers. So, what could have gone wrong? Or what could have been done differently? This is a case where something happened involving managing risks. And by risks, I mean the harm to consumers or their environment. The risk of something getting pulled under the rear roller was either overlooked (totally missed and not considered at all) or was identified and people decided that those risks were acceptable.
Something to note, here, is that there are many risk analyses, diagrams, tables, tools…they are all meant to help teams capture data about risks and make decisions. Usually, an event or effect may be an unacceptable risk if an event severity is traumatic, if it’s estimated to happen all of the time, or some other criteria of a mix of the two (the severity is high and it’s likely to happen). But we need to remember that individual people and teams of people decide if putting the product to market is worth the potential risk of harm to people or the environment.
There are three things in a risk analysis that could lead people to decide that a risk was acceptable, and it could be a combination of these things.
- For one, the severity of the effects was too low. Potential effects of injuries was not thought to be as severe as what’s being reported now. Or maybe they thought that a scrape could occur, but the field data of injuries leads to much worse than a scrape.
- Another thing in the risk analysis that could lead people to decide a risk was acceptable is the estimate of the occurrence was too low. Maybe they thought the chance of this happening was extremely remote. Or they didn’t fully understand or consider the users and the use environment, so that input was not adequately captured in their design requirement. And maybe they were also very confident in their design requirements: that they have the appropriate constraints to control the risk, which leads into controls.
- The controls for mitigating this risk were thought to be sufficient, but aren’t. Maybe they relied on the consumer to control the risk, so they provided labeling and information and thought that was sufficient to prevent harm. Based on the press release the company gave, I believe they still think this. Out of the controls, maybe there were no or not enough designed-in controls that could help mitigate or manage this risk. For example, minimizing the height of the rear roller from the floor, or integrating automatic shutoffs or alarms.
Going back to my push lawnmower example, manufacturers of a push lawnmower did put a label on the blade box saying to keep fingers away from it. But someone decided that wasn’t quite enough. So, they designed-in a control and added a switch to the motor. Now, the user needs to pull back and hold the lever against the handlebar in order for the motor to run. If they let go of the handlebar and the lever, the motor shuts off. Now, I know plenty people find that annoying and bypass that safety feature. But then we’re getting into misuse of our product.
We’ve reviewed how a risk acceptability decision could have been made: the estimated severity or occurrence was too low, or the controls were not as good as they thought. Now it’s a matter of this: we’re getting information from the field and now we’ve learned something new that we didn’t know before. The severity is more severe than we thought, or it’s happening more often than we thought it would, or the controls we put in place are insufficient. Now we need to stop and regroup. Given what we know now, do we still think the risks are acceptable? Do we still think our product is safe?
I’ll be following this story to see what happens. I suspect it may be years until it’s fully resolved.
What do we do today with what we’ve been talking about?
- Well, for one, we can recognize that use environment and user process is a really important input into the design process, not just for dependability and user experience but also for safety.
- Remember that people make decisions on if a product’s design is ready to sell to consumers. Risk analysis can help us evaluate the information so we can make the best decision possible.
- And we need to allow ourselves room to change our minds about the acceptability of a product given new information. Sometimes that’s having a contingency plan for if things turn tragic.
Now I’d like to hear from you. What is one consumer product that you use that has built-in safety features as part of the design that you appreciate? You can comment on this podcast blog at QualityDuringDesign.com, reach out to me on Linked-In (I’m Dianna Deeney), or you can leave me a voicemail at 484-341-0238. I get all the messages and I might include yours in an upcoming episode. If you like this podcast or have a suggestion for an upcoming episode, let me know. And share this podcast with your designing peers. This has been the production of Deeney Enterprises. Thanks for listening!
Leave a Reply