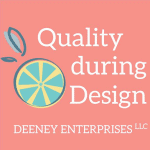
Fishbone Diagram: A Supertool to Understand Problems, Potential Solutions, and Goals
A Fishbone Diagram is named for its looks because it resembles the bones of a fish drawn on paper. Its less creative names are Cause-and-Effect Diagram and Ishikawa Diagram. It’s popularly known to help with root cause analysis. But, we can also use it to help with goals and to evaluate a potential solution.
Why is it a Supertool? Just creating its headings helps us to better define our question. Writing it out as a graphical organizer helps organize jumbled thoughts. And, when paired with a 5W2H approach and the 5-whys, it can help us dig to the root causes.
I’ve included some abbreviated examples of fishbone diagrams; click the thumbnail for a larger version (notice that my root causes follow the 5-whys). And, listen to the podcast (or read the transcript) to learn more about Fishbones and their construction and uses.



The 5W2H approach is asking ourselves this: who, what, when, where, why, how, and how much?
The 5-whys approach is asking ourselves why repeatedly until we get to the root cause: something that we can take action against and, when addressed, stops a chain of events from occurring.
Once you’ve had a chance to listen, I want to hear from you. Share your answers to this question in the comments section.
What fishbone headings have you used that are different from the examples I gave?
Citations
I used Lucidchart to create the examples shown. My tip for using this supertool: don’t drag down the process by trying to get it all lined-up pretty in software; it will stop of the flow of thoughts before you even begin. Start it with your team on paper, a virtual sketchpad, or even using sticky-notes (the real and virtual kind). You can draw it up for records later.
Other citations:
Presentation Barsalou, Matthew. “Human Factors & Root Cause Analysis.” World Conference on Quality & Improvement, ASQ, 25 May 2021.
Book Tague, Nancy R. The Quality Toolbox ASQ, 2005.
For an excerpt of Ms. Tague’s Book about the fishbone diagram, see asq.org/quality-resources/fishbone
Episode Transcript
We’re trying to solve a problem that we’re having issues pinpointing the causes for. This could be a customer complaint, a failed test, or a reoccurring issue with a process or product. This could be a big problem, a little one or even a human factors problem. Or we’re evaluating a potential solution or action and want to better understand the positive and negative effects. There’s a graphical organizer for that. What is this Supertool? A Fishbone Diagram! Listen-in to learn more, after this brief introduction.
Hello and welcome to Quality during Design, the place to use quality thinking to create products others love for less. My name is Dianna. I’m a senior level quality professional and engineer with over 20 years of experience in manufacturing and design. Listen-in and then join the conversation at qualityduringdesign.com.
A Fishbone Diagram is also known as a Cause-and-Effect or Ishikawa Diagram. It’s a graphical organizer used to help capture the many causes and effects of something. You can use it to help solve a problem, figure out how to achieve a goal, or to evaluate a proposed solution or action. Creating a Fishbone can be a systematic approach in that you step through broad categories (or buckets) of causes and identify as many as you can. The goal is to get to a root cause or to a level that we can take action against. But the way this diagram is constructed also helps us to think of ideas that are outside of our ability to change, which leads to a better understanding of the problem.
This graphic organizer is called a Fishbone Diagram because that’s sort of what it looks like: bones of a fish lying out on a piece of paper. The head of the fish is the main problem that’s being evaluated, or the goal we want to achieve, or a potential solution. Stemming from that are the bones of the fish. To the left of the head is a backbone with three or more ribs. Each rib is a major category of a problem. Typical generic headings are: measurement, materials, process equipment, people, and environment. (You may also hear quality folks refer to the 6Ms. If so, these headings are what they’re talking about.) If we’re evaluating a human factors problem, our headings could be things like: performance information (like tasks), physical situation (like workspace), individual considerations (like vision and ability), error impact, and corrective actions. The point is, we want to use headings that capture the full range of possibilities. We may end up not having any causes to collect in that category, but if it’s a category of potential source, we’re going to include it. From each rib are tributaries, further breakdowns of causes and effects until we get to the root cause. I’ll create an example of a Fishbone Diagram and put it on this podcast blog. I’ll also include a link from ASQ, which is an excerpt from The Quality Toolbox by Nancy Tague, a book I highly recommend.
A big benefit of the Fishbone Diagram is its ability to help us graphically organize thoughts in a systematic way.
It’s helpful to us to create the diagram.
- First, it forces us to define our problem or goal succinctly in a short phrase. Sometimes just doing that is a valuable exercise. Plus, it ensures that everyone involved is on the same page and knowing what the focus or problem is about.
- Second, each rib defines the major categories of potential causes. A bit earlier, I listed typical generic headings, the 6Ms. There may be a different group of major headings you want to explore. Labeling those headings gets us ready to explore causes from all the angles.
- Third, the way the causes are displayed lets us dig into and capture the root causes. For example, if we’re exploring potential causes under the environment heading, high temperature may be a cause to our issue. If we dig a little deeper, we may determine that high temperature during shipping and handling could be the culprit, and that is happening because of an incorrect carrier contract. All of these levels of causes can be captured on a fishbone diagram.
After the diagram is created, it can be used to communicate with other team members, departments, or anyone else that can help. It’s a graphical organizer that can help others quickly get up to speed. I’ve also seen it used to document a root cause analysis for test failures as a way to communicate and document that all potential avenues were investigated.
Along with Fishbone, we may hear quality practitioners talk about a 5W2H method or approach. Really, it’s an approach used to understand the situation. The 5Ws are: who, what, when, where, why, and the 2Hs are: how and how much. Using this method is a good way to slow down and ensure we’re thoroughly thinking about each cause.
You may also hear practitioners talk about the ‘5 whys’. This is a process where we ask ourselves ‘why’ multiple times until we get to the base cause. Why did the equipment fail? Because maintenance wasn’t performed. Why did the user not perform maintenance? Because they didn’t understand its importance. Why? Because they weren’t trained. Why? Because no one in that facility was designated to maintain the equipment. Why? Because our delivery an onboarding process did not follow up about the missing mandatory training. We finally got to a root cause we can take action to address our delivery and onboarding process.
What can you do with what we’ve been talking about today? Visit this podcast blog and check out what a Fishbone looks like. It’s a memorable tool and one that a lot of people can pick up on quickly. Try a Fishbone as part of your team’s root cause analysis, when you’re trying to figure out how to achieve a goal, or when evaluating consequences of a proposed action. Remember the ‘who, what, when, where, why, and how’ questions to force yourself and your team to think of all the angles. And repeatedly ask yourself ‘why’ to make sure you’re really getting to the base causes.
Please visit this podcast blog and others at qualityduringdesign.com. Subscribe to the weekly newsletter to keep in touch. If you like this podcast or have a suggestion for an upcoming episode, let me know. You can find me at qualityduringdesign.com on Linked-In, or you could leave me a voicemail at 484-341-0238. This has been a production of Denney Enterprises. Thanks for listening!
Leave a Reply