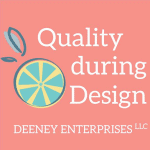
Types of Design Analyses possible with User Process Flowcharts
Flowcharting isn’t just useful for manufacturing processes. We can use them in lots of ways to help us with design of products and to identify quality characteristics. After all, products are used by people, and the way in which they use them is a process.
- compare ideal vs. actual flowcharts
- identify where there is disagreement about correct sequence or steps
- identify common mistakes/problems at each step to mistake-proof the process and design
- look for holds or delays, find the critical path
We also talk about specific flowchart analyses and how they can be used to analyze the user process for design.
- Cost-of-Poor-Quality
- Critical-to-Quality
- Value-Added Analysis
- Deployment Flowchart
We can use flowcharting to prioritize decisions. We can use lean principles (in the user process, also!). We can eliminate costs, focus on what’s most important to the customer, get to an ideal state of a user process, get alignment with who’s doing what during our process between our users, mistake-proof the user process, and identify the critical path.
Learn about this graphical tool and use it to make and prioritize design decisions for the user. We can take our detailed flowchart a step further and use it as an input into a UFMEA (usability failure mode and effects analysis).
Citations
If you are new to process flowcharting, get in touch with your local Quality Professional, or see this resource from ASQ: What is a Flowchart? Process Flow Diagrams & Maps | ASQ
Episode Transcript
The flowchart: it’s one of the seven basic quality tools, also known as the process flowchart or a process flow diagram. It’s used to define, study, and communicate a process. It’s a graphical tool. Designers need to know how to use it because of the user process. Let’s talk more about the various ways we can use flowcharting in design, after this brief introduction.
Hello and welcome to Quality During Design, the place to use quality thinking to create products, others love for less. My name is Dianna. I’m a senior level quality professional and engineer with over 20 years of experience in manufacturing and design. Listen in and then join the conversation at quality during design.com.
A flowchart is a graphic of the separate steps of a process in sequential order. It is a highly adaptable tool with several variations for how to analyze the process. Manufacturing process engineers are really familiar with this tool because they use it to help them identify, evaluate, and improve their manufacturing processes. But this flowchart is also a valuable tool for designers because as a designer we’re developing products for people to use. People are working or stepping through a typical process to use the product that we’re designing. We can use flowcharting to help evaluate that user process and pull-out important features, quality characteristics, and steps and information that the user needs in order to use our product to do the thing they want it to do.
There are common symbols used when we’re creating a flowchart: a rectangle is a process step, a diamond is a decision point, and an oval is the beginning and end of our flowchart. There are other common symbols that we can use in our flowchart. I’ll include a simple graphic of some common flowchart symbols on the podcast blog.
To create a flowchart, use a group activity experience. Plan work sessions with key people involved in the design. This could be your field ops, marketing people, design engineers, manufacturing…anyone that has a say-so in how the quality characteristics of a product are defined. You will also want to plan to gather feedback of other key people involved in your user process. Namely, your users! You can include supplier feedback and customer feedback by interviewing them before work sessions or getting feedback from them between work sessions. But make sure that you get their input, also.
If the first step is planning work sessions, the second step is deciding on the process boundaries and the level of detail. Where do you want to start evaluating process? Which step do you want to start evaluating your process from when your product leaves your shipping dock or when the customer receives it? Or, maybe when the customers opening the package? Where do you want your process analysis to end? Do you want it to end after the first use, after five years, or upon recycling and disposal?
The third basic step for flowcharting is to brainstorm in your work sessions with your key people and arrange activities in sequence. Draw arrows to show the flow; sort of keep it fluid as you’re brainstorming this process flow of your user. Finally, you want to draw the final flowchart. Here’s some advice: Don’t get hung up on trying to create your flowchart within a software package with your group during the brainstorming and creation stages. These software packages are very useful and can seem fast, but it bogs down the team in trying to make a pretty flowchart instead of really capturing the necessary and important details about your process.
Now, if we have a detailed flowchart which shows all the steps of our user process in sequence, we can start doing some fun analysis with it.
We can compare our ideal process versus the actual process. Maybe we want to compare the process between our alpha version and our beta version of our products. Maybe we’re designing the next generation of a product and we want to make it better for the user. Perhaps there’s a competitor that is well known for their device and we want to evaluate their device process and improve upon it with our own design.
With our detailed flowchart, we can also identify where there’s disagreement about the correct sequence or steps. This disagreement could be our misunderstanding of what the user needs to do, or the user expects to be able to do, or it could be a disagreement between different types of users. That would be really helpful information for us to know in advance of our design process.
With the flowchart we can identify common mistakes or problems at each step, so we can mistake proof the process. This gets into our prevention controls where we can design our product to prevent problems from happening in the first place.
With our flowchart we can analyze cycle time or look for holes or delays or find the critical path. Doing these things can help us create an efficient design and an efficient process for our user to be able to use our product. Finding the critical path could be important to us in understanding which quality characteristics we want to define and measure.
In addition to all of that, there are also four other techniques we can use, depending on what information we want to get out of our flowchart.
There is a cost-of-poor-quality flowchart, and we can use this to identify the problems, root causes, and prioritize fixing those causes based on cost. To do that, we create our detailed flowchart like we have, but we ensure that the flowchart shows how problems are handled if when using our product the user needs to make a decision or has a particular problem that they sometimes encounter, that could be a decision point where we need to capture in our flowchart: how they handle that problem or what decisions they make when faced with that problem. Then we can identify those process steps that add to the cost of quality in our user process scenario. This could be something like the product failing, or the customer needing to call the company for instructions for how to solve this particular problem, or for maintenance issues. Then we can identify those process steps that, if they’re done properly, it eliminates those costs of quality. The cost-of-poor-quality flowchart analysis can help us identify those prevention controls.
Another specific analysis we could do with flowcharts is the critical-to-quality analysis, where we identify quality characteristics that are important to the customer, and we also use it to find problems. So again, we start with our detailed flowchart which shows the steps critical to achieving quality. We study the output side of our flowchart of our process. We list our customer’s needs. Is it that it needs to be on time? That it is easy to use? That it produces a correct output? We ensure we answer the who, what, when, where, and how of the output of our process. Then we study the input side of our process in a similar way. What are the inputs that are needed for this process? And, again, we want to answer the who, what, when, where, and how? Then, we can identify the critical to quality steps, where we identify where the quality of the output is affected, either hurt or helped. At what point during our process does the input determine what happens next in process? And, what are those critical-to-quality steps that we can measure if the inputs and outputs are meeting needs? With these identified, we can study them to further identify other problems for prevention or detection controls.
Another type of flowchart analysis is value-added analysiswhere we identify the individual steps that add value for the customer. Is it necessary to produce output? Does it contribute to the customer satisfaction? If so, then we color those steps green. Then we identify those steps that provide organizational value. If it contributes to the organizational needs, then we’re going to color it yellow and study to reduce or eliminate it. Perhaps part of the user process that we’re evaluating is the user providing warranty information back to us. That could be an organizational need that we would want to reduce or eliminate or make easier for the customer. Then, in our detailed flowchart, we also identify the non value-added steps, we color those red, and we want to study to reduce or eliminate those steps altogether.
The last type of flowchart analysis I’ll cover today is a deployment flowchart. This type of flowchart uses swim lanes to identify relationships, communicate responsibilities, and study how parallel steps affect time. If you have a medical device that needs both a physician and a nurse to interact with it during the procedure, you could use a deployment flowchart to identify which steps the nurse is taking and which steps the doctor is taking.
I think Flowcharting is a lot of fun, but it’s also one of my tools that I keep in my back pocket, and I use it quite often. I can use it to prioritize decisions. We can use lean principles (in the user process, also!) We can eliminate costs, focus on what’s most important to the customer, get to an ideal state of a user process, get alignment with who’s doing what during our process between our users, mistake-proof the user process, and identify the critical path. And we can take our detailed flowchart a step further and input it into a usability FMEA where we are evaluating potential failures, their effects, and their causes and what we’re doing to control them.
What’s today’s insight to action? Check out flowcharting as one of the design tools you can use to gather inputs into your design process. Use it to communicate with customers and users about how they’re going to use your product. This information is vital to the success of our designs.
Please visit this podcast blog and others at quality during design.com. Subscribe to the weekly newsletter to keep in touch. If you like this podcast or have a suggestion for an upcoming episode, let me know. You can find me at quality during design.com on LinkedIn or you could leave me a voicemail at 484-341-0238. This has been a production of Denney Enterprises. Thanks for listening!
Leave a Reply