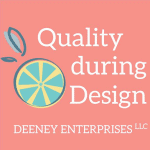
The DFE Part of DFX (Design For Environment and eXcellence)
Design for Excellence (DFX) is a concept that includes many initiatives, like design for usability, design for manufacturability and assembly, and design for environment and disassembly. It’s a focus on doing things right, exceeding customer expectations, optimizing what’s needed while minimizing costs, and continuous improvement.
Today we take a deep dive on one of those aspects: design for environment (DFE), including design for disassembly. What are reasons that a business would consider this important, and how does a design engineer fit in?
What actions can we take today, right now?
With where you work, look into the company’s policies about design for environment or design for disassembly. If they don’t have one ask, “Why not?” Consider the life cycle costing, marketing, and customer relationship aspects.
Consider incorporating some design requirements for environment and disassembly. You may be surprised to find that the regulations or standards that your design needs to meet specifies labeling and waste requirements, too. Different countries and regions may have different regulations about disposal, so keep that in mind.
Think about other users besides the person using the device. Could there be other users, like repair people? Or, people that need to break down a device for recycling and repurposing? Consider including those users into your usability engineering efforts.
Citations
And do some reading about where trash goes. It can give you some ideas about how you can better design for environment. Here’s my suggestions:
Book: Royte, Elizabeth. Garbage Land: On the Secret Trail of Trash. United States, Little, Brown, 2007.
Website: EPA (United States Environmental Protection Agency): “Facts and Figures about Materials, Waste and Recycling” www.epa.gov/facts-and-figures-about-materials-waste-and-recycling
There’s some previous episodes of the Quality During Design podcast that explores some of today’s concepts further:
Episode 32 “Life Cycle Costing for Product Design Choices“ explains the calculations and offers equations, resources, and examples.
Episode 24 “Why Look to Standards” talks about regulations for repair of products and how standards can be applied to design. They could help with keeping a design simple with components that can be reclaimed.
Episode Transcript
Design for Excellence (DFX) is a concept that includes many initiatives, like design for usability (or Ux), design for manufacturability and assembly, and design for environment and disassembly. It’s a focus on doing things right, exceeding customer expectations, optimizing what’s needed while minimizing costs, and continuous improvement.
Today we take a deep dive on one of those aspects: design for environment (DFE), including design for disassembly (DFD). What are reasons that a business would consider this important, and how does a design engineer fit in? Let’s talk more about it, after the introduction.
Hello and welcome to quality during design the place to use quality thinking to create products others love, for less. My name is Dianna. I’m a senior level quality professional and engineer with over 20 years of experience in manufacturing and design. Listen in and then join the conversation at QualityDuringDesign.com.
Consumers are considering the environmental and long-term costs of products. I do. I no longer buy stuff that I think I’m going to have to junk once it’s broken. I’d rather spend a little more money on something that can be repaired or refurbished…something that will continue to have value after it’s broken. And I try to use products that multi-task with other things that I have. It’s a measure of quality that I look for in what I buy.
I don’t want to buy and store a snowblower because it’s yet another thing I have to perform maintenance on and fix if it’s broken. But I will buy a snowplow and tire chains that fits onto the lawnmower I already have. I’m already maintaining my lawn mower and using it through the cold winter months for plowing snow makes sense.
I steered my kid away from the video game consoles, which are notorious for not being able to be repaired. Plus, a new model comes out with new games…their lifetime value is not very high in how my household would use it. Once a new model is available, the resale is terrible. Oftentimes, our option would be to just throw it away. I instead encouraged him to get a gaming PC (personal computer), something that he could update when he needed to. He could update the graphics card and add different inputs. If his fan breaks, he can open the computer case and replace it. Plus, he can do more with it (like his homework).
One last example, my 20-year-old clothes washing machine broke. I tore it apart, did some investigating, and learned that the agitator part that I’d need to replace cost more than a new machine. Just the part, not the labor (because I was doing it myself). I could still tear it apart into pieces for salvage or recycling. I had no regrets with that machine…It lasted a long time, and I knew it wouldn’t just end up in a junk heap. If it weren’t repaired, it could at least be recycled or salvaged.
Design for environment not only considers things like the types of materials we choose and their supply chain, but also involves designing for disassembly and recycling. Part of understanding design for environment and disassembly is getting a better understanding of what happens with our products after their useful life. What trash stream does it get put into? Where does it go and how is it transported? How is it handled (does it get sawed open and broken down, or does it get repaired)? Who handles it?
Design for environment and design for disassembly are not opposing forces to being cost-effective with a design that is built with quality that is safe, reliable, and user-friendly. And, I think in many cases, designers can incorporate design for environment and disassembly into their products, especially when we keep that in mind from the start. It may take purposeful choices, ingenuity, and a little creativity. Some on our team may say, “I don’t care what they do with the product after it’s broken or used.” If your team is not concerned with waste, then there are other perspectives to consider to weigh the benefits of DFE and DFD.
One perspective is to look at costs. Within our life cycle costing, we should consider the end-of-life costing. With regulations and the need to manage device waste being pushed to manufacturers, it may be an easy choice to reduce end-of-life costs by using DFE.
We’ll have lower disposal cost because we have a better end-of-life value: products can be taken apart for their components for repair or salvage.
We’ll have reduced regulatory costs, because we now may not have to monitor and dispose of hazardous components at the end of our product’s life (like lithium-ion batteries). Or we won’t’ need to develop and maintain an end-of-life product return system (like for electrical products).
And, we’ll minimize liabilities for our involvement in waste management.
Another perspective from which we can look at DFE and DFD is from a marketing perspective. We can use those concepts to improve relationships with our customers. Or, as a way to keep in touch with our customers and continue to provide value and services after a product sale. These are business revenue streams that are outside of the sale of the product but could still positively impact the business.
If we use design for disassembly, then we can use that to develop long-term relationships with repair houses or direct-to some customers that repair their own things (like me).
We can become a partner with our customers in being mindful to environmental issues. Customers don’t like managing these wastes on their own, and sometimes they just cannot manage them on their own. Having a ‘partner’ in the device manufacturer would be a high-value thing. I like when there’s a label on the product that says, “for disposal, visit this website or call this number”. Or, having the symbols for what is recyclable and what is not. I consider these types of things when making purchases.
I also like certain retailers and buy products from them because I appreciate that they help me recycle or dispose of my electronic waste.
Design for disassembly and environment may fit into efforts for the design for manufacturability. In design for manufacturability, we look to create product designs that are easier and more efficient to produce. But we don’t want to create designs that are easy to produce but then difficult or too expensive to repair. We also don’t want to use components that are complex, which aligns with being able to disassemble and repurpose parts for design for environment and disassembly. One of the guidelines for design for manufacturability is to minimize the number of parts, and that aligns with design for environment, too. The guidelines for design for manufacturability are not competing with guidelines for design for environment or disassembly.
With product design, we have all the choices we can make with how things are designed. Here are just 5 examples:
Can we reduce the number of components without using more complex componentsand without sacrificing the safety, durability, and usability of our product? Maybe components are quickly assembled using spot welding, glue, or rivets. Can we design for disassembly, instead using screws? Or, can we get rid of most of the extra components with a different housing design? Less components, less complex, easier to disassemble… Do we have one product that is used once and thrown away? Can we separate the functions of the design into different products: one part that is disposable and the other that can be reused multiple times?
Can we be more picky with where we’re getting materials and components? Are there suppliers that we can build long-term relationships with that have the same or similar goals for design for environment?
We can design for different users: the consumer, the service or repair person, and the disposer. At each lifecycle step, there may be different users with different needs. Like my washing machine example, there could be user requirements for everyday use of the washing machine, different user requirements for the repair person to disassemble and repair the unit, and different user requirements, still, for the person that is responsible for disassembly and proper disposal of any hazardous materials.
Our designs can consider and separate different waste streams. Do we have a product where one part will be a biohazard waste, and the other electronic waste? Can we separate the design so each part can be separately disposed of properly, instead of throwing it all into one waste stream?
And, lastly, we can choose materials and components that can be recycled. Thermoplastics can be recycled; other types of plastics cannot. Cardboard packaging is easier to recycle than foam packaging.
What’s today’s insight to action?
With where you work, look into the company’s policies about design for environment or design for disassembly. If they don’t have one ask, “Why not?”
Consider incorporating some design requirements for environment and disassembly. You may be surprised to find that the regulations or standards that your design needs to meet specifies labeling and waste requirements, too. Different countries and regions may have different regulations about disposal, so keep that in mind.
Think about other users besides the person using the device. Could there be other users like repair people, or people that need to break down a device for recycling and repurposing? Consider including those users into your usability engineering efforts.
And do some reading about where trash goes. I’ll include some links on the podcast blog for further reading.
There’s some previous episodes of the Quality During Design podcast that explores some of today’s concepts further:
Episode 32 “Life Cycle Costing for Product Design Choices“ explains the calculations and offers equations, resources, and examples.
Episode 24 “Why Look to Standards”, talks about regulations for repair of products and how standards can be applied to design. They could help with keeping a design simple with components that can be reclaimed.
Please visit this podcast blog and others at qualityduringdesign.com. Subscribe to the weekly newsletter to keep in touch. If you like this podcast or have a suggestion for an upcoming episode, let me know. You can find me at qualityduringdesign.com, on LinkedIn, or you could leave me a voicemail at 484-341-0238. This has been a production of Denney Enterprises. Thanks for listening!
Leave a Reply