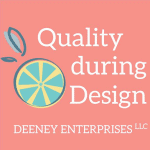
How can 8D help Solve my Recurring Problem?
We talk about the 8D methodology, describe situations where we could benefit from it, list each of the 8 Disciplines, and compare it to PDSA and DMAIC.
The 8D method of problem solving might be the perfect method for our team to use if:
- we’ve had a reoccurring problem that’s noticed later than when it’s created
- the issue is a repeat because it wasn’t solved the first time – we need a strategic approach to solve the problem once and for all
- we need ways to involve stakeholders throughout the project for awareness, to provide focus, and for resources
- we want to learn from the failure and apply the results to other areas of our organization
8D is a prescriptive, step-by-step method that calls for a team to approach the problem-solving method as a means toward mastering each of its 8 Disciplines (while solving a problem). For that reason, the success of using the 8D methodology is dependent on the team members and the culture within the company that it is used. If your team is growth-minded and your organization supports the team’s problem-solving efforts, using 8D could be a good opportunity to grow in quality – for each team member and the business itself.
Citations
If you’re new to 8D, see this website glossary entry from ASQ: What is 8D? Eight Disciplines Problem Solving Process | ASQ
If you’re ready to dive-in, or need a refresher, I recommend this book:
Visser, Chris S.P. 8D problem solving explained: Turning operational failures into knowledge to drive your strategic and competitive advantages, 2nd ed., in2quality, 2018.
Chris Visser also has a website with other downloadable files to help with 8D – www.in2quality.com. The templates pictured are from this site.
Episode Transcript
What is 8D? Now, we’re not talking about 8 dimensions and things like quantum physics. We are talking about a quality tool, a system and a methodology for fixing a problem. So, what is it? How does it compare to some of the other common continuous improvement and problem-solving methods? And when we want to use it? Let’s learn more about this tool after the brief introduction.
8D is short for “eight disciplines”, and it’s a model: “the eight disciplines model”. According to ASQ, it’s “a problem-solving approach to identify, correct and eliminate recurring problems.” The eight disciplines method was started in the automotive industry, but it has been used successfully in a lot of other industries, also.
What makes 8D special or different from the other models that we may be used to? 8D is a stepwise approach, meaning we have to execute steps in sequential order because output of one step is an input into the next. Each step is considered a discipline itself to be mastered, and that will become more apparent as we talk about what each “D” means. There is a clear beginning and end to this model (it’s not a cycle of continuous improvement). And it’s supported by a report tool, and this reporting tool summarizes the investigation as it’s being performed. The reporting tool is prescriptive about what type of information we should be analyzing or reporting on at each discipline step. It’s to allow us to reflect on the analysis as we’re performing it. It also creates a single project document which is good to have for posterity and historical references for when a similar issue should arise. It is also used to communicate with an external supplier or customer. The reporting tool provides consistency in both the method and also where what type of information is located within the report, which makes it easier for reviewers.
As you’re probably already guessing, based on the sequential nature of this method and also the strict reporting styles and reports that are used, the 8 Disciplines problem solving method is sort of strict and prescriptive. This could be a benefit to an organization, and it could also be a detriment to an organization. It really also depends on what type of problem you’re trying to solve and how your team likes to function and work.
There are some things to consider when we’re deciding whether to use an 8D method to react to an issue. One thing to consider is: is our failure created earlier in the process, but notice later? If so, this issue could be an ideal candidate to be resolved with the 8D method. Have we seen this problem before? If it’s a repeat issue, then we didn’t fully learn or fix what we needed the first time. A more disciplined approach and a more stepwise sequential approach to problem solving might help us for good this time. Is our primary objective learning from failures? If we want to better understand an issue, its resolution, and be able to apply it to a broader set of problems then the discipline of the 8D method might help us do that. It may help us derive the strategic and competitive advantages that we’re looking for in solving the issue. And lastly, do we need to communicate that status with stakeholders. That could be internal stakeholders, customers, or our suppliers? If yes, we want to follow model to routinely summarize the activities so that we can create awareness, provide focus, and check that resources are available. The 8D model can do this for us.
What are each of these eight D’s or disciplines? Chris S.P. Visser authored a published a book in 2018 called “8D Problem Solving Explained: turning operational failures into knowledge to drive your strategic and competitive advantages.” It is a very clear and straightforward how-to guide about using the 8 disciplines methods. I mention his book because he specifically created a handy graphic about the process. It looks like a stopwatch, and I think it’s a great visual of how the 8D process works. The stopwatch shows the sequential disciplines and how they interact with each other. I’ll post a picture of it on the podcast blog.
Let’s talk about the 8 Disciplines and I’ll describe how they fit with respect to the stopwatch. The 8 Disciplines model started as 8 disciplines. But, then as people used it, they decided to add a prerequisite discipline which is planning. The Planning Discipline is not shown on our stopwatch graphic, but we are planning to solve the problem and we’re also defining prerequisites for our project. We’re also identifying the need for any emergency response actions that we need to take to contain and control the issue that we’re going to be fixing.
The First Discipline is to create a team. We’re establishing the 8D team and we define the team roles. This discipline is the body of the stopwatch – it encircles all the other disciplines and steps in this methodology. That’s because there might be particular team members that have influence and experience at some steps, but maybe not others. We’ll have to bring in different team members at other times during the method. We’re always considering and evaluating if we have the correct members of our team to solve the issue.
Discipline 2 is to define and describe the problem. Discipline two makes up the center of our stopwatch graphic, where the minute hands would be mounted. That’s because the whole process is centered around solving this issue. Discipline 3 is about containing the problem, where we need to develop those interim containment actions. What are we doing to address the bad customer reactions and experiences? What are we doing to prevent bad product going out into the field? How are responding to the issue that we’re seeing? Our containment actions continue throughout the 8D model until we’ve taken preventive measures. So, discipline 3 spans discipline 4, 5, and 6 on our stopwatch model.
Discipline 4 is to identify, describe, and verify root causes and escape points. Discipline 5 is for us to choose permanent corrective actions and to verify that they resolve the root cause and the escape points. Discipline 6 is to implement and validate those permanent corrective actions, essentially solving the problem statement. Discipline 7 is to take preventive measures where we’re preventing recurrence, including similar processes. And Discipline 8 (which is last, but not least) is to congratulate our team. We’ll have meetings to discuss the before and after comparisons, any lessons learned, archive the 8D report, and then celebrate!
How does 8D compare to some other quality models for solving problems? Let’s compare it with the Plan-Do-Study-Act. The PDSA is meant for carrying out a change, whereas the 8D is problem solving for recurring issues. PDSA is closely into the scientific method, where we make a hypothesis, we test it, and then we make a conclusion and take action against it. The 8D model is more related to project management. PDSA is iterative, continuous improvement cycles, whereas the 8D is linear, with a defined beginning and end. The PDSA is for quick wins, where the 8D model focuses on the most effective solution the first time.
The 8D method could also be put side-by-side with Define Measure Analyze and Control, that problem solving and proven method that is famous with six sigma practitioners. The steps are basically the same, except 8D gets into some more prescriptive activities. There are five defined sections for DMAIC versus the 8 to 9 for the 8D model.
A criticism of the 8D method is that teams can develop “pencil whip” with the detailed forms. This is when we have such big forms that need so much information that we just kind of fill it in as quickly as we can so that we can move on to the next discipline. When, really, the intent of the form is get us to stop and assemble and really master that step or that discipline to be able to have lasting, long-term effects. For that reason, the success of using the 8D methodology is dependent on the team members and the culture within the company that it is used. Mr. Visser also created templates of 8D reports that I’ll post links to on the podcast blog.
What’s todays insight to action? If you’ve got a reoccurring problem that you want to finish for good, and you need a strategic approach to solve the problem and apply it to other areas of your organization, then the 8D method of problem solving might be the perfect quality tool for your team to use.
Remember to check out the podcast blog at QualityduringDesign.com to see the 8D stopwatch graphic and to download some sample forms.
Please go to my website at QualityDuringDesign.com. You can visit me there, and it also has a catalog of resources, including all the podcasts and their transcripts. Use the subscribe forms to join the weekly newsletter, where I share more insights and links. In your podcast app, make sure you subscribe or follow Quality During Design to get all the episodes and get notified when new ones are posted. This has been a production of Deeney Enterprises. Thanks for listening!
Leave a Reply