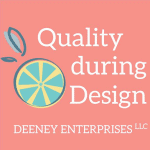
Overlapping Ideas: Quality, Reliability, and Safety
We’ve identified safety concerns about our product design. How concerned do we need to be about quality while we’re determining root causes? There is an intersection of quality, reliability, and safety. Let’s talk about how they fit together.
Think of quality as necessary for your product. We realize that quality is subjective, depending on the industry in which we work and our customers. But it is also arching over everything that we do with product design, including reliability, safety, performance, and usability. It ensures that the activities we do to develop product are in-line with customer needs (both stated and implied) through analysis, test, monitoring, and control. If we frame quality in this way during product design, we can help ensure our products are safe, dependable, and easy to use.
Citations
Visit Episode 48: Risk Barriers as Swiss Cheese? to hear more about this model of risk barriers.
Episode Transcript
We’ve identified safety concerns about our product design. How concerned do we need to be about quality while we’re determining root causes? There is an intersection of quality, reliability, and safety. Let’s talk about how they fit together.
Hello, and welcome to Quality during Design the place to use quality thinking to products others love, for less. My name is Dianna. I’m a senior level quality professional and engineer with over 20 years of experience in manufacturing and design. Listen in and then join the conversation at qualityduringdesign.com.
There is an intercept of quality, reliability, and safety. But first let’s talk about each one, individually. Quality is defined in Merriam-Webster as “a high level of value or excellence”. Really, it’s a subjective measure and dependent upon the business and its customers’ expectations. The definition of quality for a high-end clothing manufacturer is going to be different than for a fast-food restaurant chain. Even within the same industry, there are different definitions of quality for different businesses. A technical definition from ASQ is that quality is “the characteristics of a product or service that bear on its ability to satisfy stated or implied needs”. We can also think of quality as conformance to requirements or standards.
No matter what definition we use, I think we can agree that there’s an alignment of customer needs with the service or product offered. And when that alignment occurs, we have a quality product or service. For product design, this means that what we make is what the customer needs. We measure this directly through our customers’ feedback from using prototypes and production models. But we also measure this through use of tests of our product compared against the requirements, the requirements which we derived from interpreting our customers’ needs. We also measure quality of our product against the product specifications and tolerances that we created ensuring that we’re making the product right. The right concept, a solid design and repeatable manufacturing production is what makes quality product.
Reliability, according to Merriam-Webster, is “something that’s able to be trusted to do or provide what is needed.” From ASQ, their technical definition of reliability is “a probability that product, system or service will perform its intended function adequately for a specified period of time or will operate in a defined environment without failure.” I’ve also heard it described more simply: that reliability is quality over time. How well does our product maintain its original level of quality over time through various conditions? Measures of reliability are failure rates (or another name for that is hazard rates) and probabilities of failure.
Safety is “a state of not being harmful or dangerous,” according to Merriam-Webster. And from ASQ, it’s “the state of being free from harm or danger.” Those are pretty similar. If we think back to our Swiss Cheese Model that we discussed in a previous episode, there are layers of controls, actions or policies represented as layers of Swiss cheese. Each layer of Swiss cheese has holes representing failures or shortcomings in our barriers. There’s an arrow that represents a potential of harm. If the holes and our barriers align just right, and the arrowhead makes it through all the slices of Swiss, it means that the risk barriers failed, and the harmful event was allowed to happen. To minimize harmful events from happening, we can think of quality and reliability as affecting those layers of cheese. If our quality full alters, the holes in our cheese can change and can potentially let our arrow through. If our reliability is insufficient, then we might lose a slice of cheese, altogether. Quality and reliability can be measures of the continued safety of our product. Quality and reliability are more than safety though. They are also measures of functionality, desired performance and usability. All of which are also important to our customers.
Back to our original challenge, at the top of this episode. We’ve identified safety concerns about our product design. How concerned do we need to be about quality while we’re determining root causes? The answer is we should be very concerned about quality because it oversees everything. If our product is in the field, several things could have happened relating to quality. We didn’t control the quality of our product as it was made either from our raw material suppliers or our own production processes. We didn’t test the product appropriately. Maybe our test method was not valid, or flawed. We may not have created the correct technical specifications, or we didn’t create requirements that match up with our customers’ needs, including not correctly capturing the use environment of our product. All of these things should be checked as part of quality for our product design. A lapse in any of them could have led to a safety issue in the field.
At QualityduringDesign.com, in this podcast blog, I will include a graphic of how I think of quality, reliability, and how it’s associated with safety, usability, and performance.
What’s today’s insight to action. Think of quality as necessary for your product. We realize that quality is subjective depending on the industry in which we work and our customers. But it’s also overarching over everything that we do with product design, including reliability, safety, performance, and usability. It ensures that the activities we do to develop product are in line with customer needs, both stated and implied, through analysis, test monitoring and control. If we frame quality in this way during product design, we can help ensure our products are safe, dependable, and easy to use.
Please go to my website@qualityduringdesign.com, you can visit me there. And it also has a catalog of resources, including all the podcasts and their transcripts. Use the subscribe forms to join the weekly newsletter, where I share more insights and links. In your podcast that make sure you subscribe or follow quality during design to get all the episodes and get notified when new ones are posted. This has been a production of Deeney Enterprises. Thanks for listening!
Leave a Reply