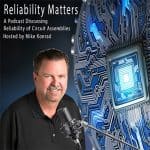
The Truth Behind Statistics
Statistics, at its core, is the science of making sense of data. From predicting trends and making informed decisions to ensuring quality control and optimizing processes, the applications of statistics are vast and varied. In the electronic assembly industry, where precision and reliability are paramount, statistical techniques become indispensable tools for engineers, manufacturers, and quality assurance professionals alike.
Join us as we unravel the complex yet captivating connections between statistics and the truth. We’ll delve into real-world case studies, and uncover the statistical principles that ensure the decisions we make every day are based on facts, accurate data, and accurate statistics.
In today’s episode, we’re also going to tackle some common myths associated with statistics and shed light on how misinterpretation of data can lead to false conclusions. Many people think of statistics as infallible, a definitive answer to every question posed by data. However, this couldn’t be further from the truth. Statistics is a powerful tool, but its effectiveness hinges on proper application and interpretation.
We’ll discuss myths such as “Correlation equals causation,” where the mere relationship between two variables is often mistaken for one causing the other. We’ll also address the misconception that a larger sample size always guarantees accurate results, and how ignoring the context or the source of data can lead to misleading outcomes.
Moreover, we’ll explore real-world examples where statistical missteps have led to costly errors and how these pitfalls can be avoided through rigorous analysis and critical thinking. By understanding these common misconceptions and learning how to approach data critically, you’ll be better equipped to harness the true power of statistics.