
High Precision Planning and Maintenance
Abstract
Philip and Fred discuss new shiny objects and why digital twins and IIOT will not solve your core problems.
High Precision Planning (HPP) supports High Precision Maintenance (HPM) which is a program running in elite industries today.
The emphasis on HPP is an absolute requirement to achieve HPM.
The benefits of achieving HPM have been demonstrated to be an improvement up to 250% in first-pass quality.
Key Points
Join Philip and Fred as they discuss HPP and HPM
Topics include:
- A special focus on Precision
- Deployment of LEAN principles to remove waste from the maintenance delivery cycle.
- Purposeful reduction in variability in the way a maintenance technician performs a specific job
- Goal is “Every Technician does the same job the same way”.
The obvious deliverable is to remove maintenance induced failures and to ensure the maintenance strategy deployed actually suppresses the failure modes expected.
Enjoy an episode of Speaking of Reliability. Where you can join friends as they discuss reliability topics. Join us as we discuss topics ranging from design for reliability techniques to field data analysis approaches.
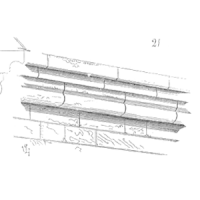
- Social:
- Link:
- Embed:
Show Notes
Given the example of typical shaft alignment what can we learn relative to HPP and HPM?
- Write down your alignment plan
- Make darn sure all the shims, bolt torques and sockets, or hex keys needed are part of the plan.
- With HPP engaged, we do not accept an empty box if shims – it must be restocked with all sizes and ready for each use.
- We need to determine what bolt torques are specific to the base bolts and coupling bolts.
- Where locking devices can be used, they should be – Nordloc is preferred based on Junkers machine testing
- We obviously need a torque wrench to ensure the torque applied satisfies the bolt specifications for tightness.
- All couplings are NOT the same!
- Some couplings require tighter tolerances to allow the bearings on each side of the coupling to survive.
Work Force Amplification
- With planning Typical lore is 3.5X work can be accomplished with the same crew.
- Philip’s experiment in Asia revealed this may be as high as 11X with HPP engaged!
- With HPP we counter the myth that every technician knows how to install every part.
- A typical factory has ~ 30,000 parts in the storeroom
- It is unrealistic to expect every technician every time to install 30,000 different things extremely well.
Its a long Game
- Operations Managers are incentivized to perform today – this shift.
- Precision concepts like shaft alignment extend asset life to > 5 years
- Its therefore a long game
- Benfits include
- Low wear
- No indusced quality problems
- Get it right the first time and it will serve you well.
- Dig out of reactive world.
- Benfits include
- Its therefore a long game
- Kitting Up work ensures it gets does with HPP Precision
- So important to remove waste from the daily work force
- Infers planning beyond what we are used to.
- Average industrial technician performs ~2 jobs per day.
- If we have 100 technician’s we can expect 200 jobs per day.
- If we adhere to the golden rile of 80% proactive and 20% reactive work as the transition to first quatile performance
- We need to plan 160 jobs a day 🙁
- So we must accept incremental planning each time we do a specific job
Leave a Reply