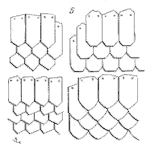
ALT Considerations Using Thermal Cycling
Abstract
Andre and Fred discuss a few considerations when conducting thermal cycling accelerated life testing.
Key Points
Join Andre and Fred as they discuss
- Know your coefficient of thermal expansion values
- Most products experience thermal cycling, with unique failure mechanisms
- The importance of running/testing the product during testing
Enjoy an episode of Speaking of Reliability, where you can join friends as they discuss reliability topics.
Join us as we discuss topics ranging from design for reliability techniques to field data analysis approaches.
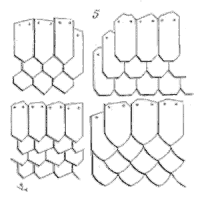
- Social:
- Link:
- Embed:
For a product which must be running and monitored during test, how do you take into consideration the impact of test fixtures on the product when undergoing thermal testing?
Hi Taylor,
Good question – as in a thermal chamber we are interested in the temperature of the product under test, not the chamber set point. Also, a powered unit may have a range of hot or cold spots across the product. The effect of thermal cycling is often to accelerate the damage due to differences in coefficient of thermal expansion, so review the board for the highest mismatches (large components, sockets, etc.) and place thermal couples on those elements in order to determine when those “likely to fail” parts reach the target temperature indicating the start of the dwell time.
The fixtures generally add to the thermal mass that the chamber has to heat/cool. Minimizing fixtures, using open racks, making sure the air flow has not dead spots, all help you change the product under test temperatures efficiently and uniformly.
Focus on controlling the temperature of the units, specifically the critical elements of the unit, under test.
Cheers,
Fred