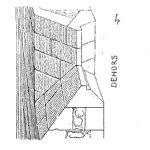
Are You Doing Root Cause or Assigning Blame
Abstract
Tim and Fred discuss the tendency to look for quick answers when analyzing quality failures, often overlooking the true root cause which may have more to do with internal culture.
Key Points
Join Tim and Fred as they discuss the difficulties in assigning root cause of a part failure, and why it’s important to consider other possibilities before blaming your supplier.
Topics include:
- Why expanding the supply base does not necessarily lead to higher quality
- Why the part that failed is not necessarily the cause of the failure
- Why you can’t count on your customers or your customer support team to help understand root cause
- When your own mixed messages about cost and delivery schedules may be the true cause of quality problems
- Are we creating conditions that make it easier for people to make mistakes?
Enjoy an episode of Speaking of Reliability. Where you can join friends as they discuss reliability topics. Join us as we discuss topics ranging from design for reliability techniques, to field data analysis approaches.
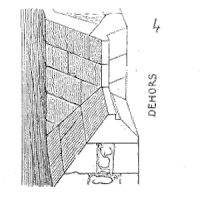
- Social:
- Link:
- Embed:
Show Notes
See also Tim’s blog post on this topic at:Â http://wp.me/pwlkj-NN
This is a great topic for discussion. Reliability cuts across all stages of part production and service. Quality and failure control/assessment is essential throughout the part life cycle. A technological system model is needed to evaluate all inputs and outputs. This will stop any blame and misunderstanding. Technological inheritance model can be helpful.
Hi John,
Thanks for the comment. The link you added was to the homepage. Do you have a link to the idea of technological inheritance model you mention?
Cheers,
Fred