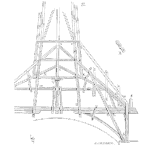
HALT Sample Size
Abstract
Kirk and Fred discussing the challenge of getting samples to test during product development. Early prototypes of new products are typically scarce, expensive, and in high demand to many engineering teams to test. HALT testing requires pushing the product to operational limits and discovering what will fail which is scary for management and engineers that do not understand the value of information that is discovered with empirical limit tests.
Key Points
Join Kirk and Fred as they discuss the importance of getting the most valuable information from each sample used for HALT.
Topics include:
- Methods of finding additional limits after the first limiting device is discovered and overcoming inherent limits such as thermal protection circuits.
- How wide differences in limits between samples may give useful information about manufacturing variation in the products strength distributions that lead to reliability risks
- What stage of development status of hardware is needed to start HALT and how HALT should be applied to some vendor subsystems before the system hardware is ready.
Enjoy an episode of Speaking of Reliability. Where you can join friends as they discuss reliability topics. Join us as we discuss topics ranging from design for reliability techniques, to field data analysis approaches.
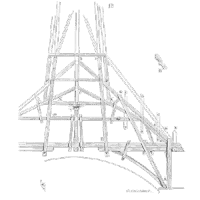
- Social:
- Link:
- Embed:
Show Notes
To find out more about Kirk’s Reliability Consulting services, please follow this link to his website Accelerated Reliability Solutions
Here is a link to Kirk Gray and John Paschkewitz’s new book “Next Generation HALT and HASS: Robust Design of Electronics and Systems”
Hi Fred;
In IPC 9592A Table 5.1 for All Classes and Categories, Minimum Sample Size for HALT Tests are: 3 for Low Temperature Step Test; 3 for High Temperature Step Test; 3 for Rapid Thermal Cycling Test; 3 for 6-DOF Random Vibration Test; 3 for Input Voltage Test; 3 for Output Load Test; 3 for Combined Stresses Test