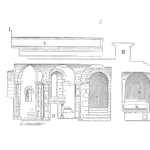
How Much is Reliability Dependent on the Design, the Manufacturing, and the Customer Use Conditions?
Abstract
Kirk and Fred discussing the many causes and contributors to products failing after purchase. How do we know which factors are the largest contributor to causing failures?
Key Points
Join Kirk and Fred as they discuss they question everyone would like to know before they purchase a electronic product, that is “how long will it last?”.
Topics include:
- What can engineers do to understand the underlying causes to failures besides the counting the returns?
- Is the design of the product always the ultimate cause of failures, since design for manufacturing and the variation in manufacturing and field use should be built into the design?
- The GM ignition key and airbag failures are a well documented case history of multiple chains of failure of design and testing.
Enjoy an episode of Speaking of Reliability. Where you can join friends as they discuss reliability topics. Join us as we discuss topics ranging from design for reliability techniques, to field data analysis approaches.
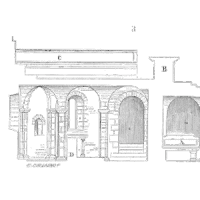
- Social:
- Link:
- Embed:
Show Notes
Click HERE to read Kirk’s LinkedIn article on the failure of GM to find and fix its airbag and ignition. It is titled “Will GM add a Fish Scale to its Reliability Toolkit?”
For more information about Kirk’s Consulting services, please see his Accelerated Reliability Solutions website please click here
To see or purchase Kirk’s new book co-authored with John Paschkewitz, “Next Generation HALT and HASS: Robust Design of Electronics and Systems” please click on this link.
We always appreciate your feedback, suggestions and questions.
Thanks for listening.
very helpful discussion, thanks!
Thanks Don!
Thank you so much for this active and productive discussions. I did a research work on the conditions of design and manufacturing as well as how it affects life and reliability. All the different operations are interrelated with each other and also with the product and manufacturing processes. Different production line can be used to produce the same quality requirement of the same finished product. For example finished critical machine parts by grinding and turning, which results in the same surface roughness of 0.02 micrometer and with the same life-time (10 yrs) for wear resistant purposes. During customer optimum use conditions, they all failed at different times, instead of failing at the same life-time. The research also found that the finishing manufacturing operations were the most influential to the quality of product. Due to the method used for design requirements selection, which sometimes is not based on component or system condition optimization for standard requirement, it may therefore end up in sub-optimal design.
There is a multi-variate model to describe and determine the influence of the different processes on the quality, life and reliability of components and system. The optimized data is used to set up a standard requirement for design, manufacturing and maintenance. See my book titled “integrated Reliability; Condition Monitoring and Maintenance of Equipment”
Thanks John for your comment.
You illustrate one of the many slight variations that may significantly change the life entitlement of a component in a system.