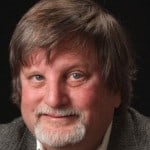
Policy – Minimum Acceptable Failure Analysis
Abstract
Kirk and Fred discussing when a failure rate of a product is acceptable or not acceptable.
Key Points
Join Kirk and Fred as they discuss how levels of criticality of different cases of failure help determine the level of failure analysis, effort and cost to fix it.
Topics include:
- Some failures are worth the cost and expense of a a deep dive, but it can be hard to determine when it first occurs.
- Changes by the procurement purchasing cheaper components during production is a constant potential for components that cause failures even though the component specifications are the same.
- Fish-bone diagrams can help determine likely causes of failure and isolate the root cause of failure, sometimes requiring invasive or destructive that can destroy the evidence of the cause.
Enjoy an episode of Speaking of Reliability. Where you can join friends as they discuss reliability topics. Join us as we discuss topics ranging from design for reliability techniques to field data analysis approaches.
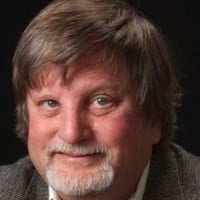
- Social:
- Link:
- Embed:
Show Notes
Here is a link to Kirk’s book co-authored with John J. Paschkewitz available from Amazon “Next Generation HALT and HASS: Robust Design of Electronics and Systems”
Here is the link to the US ARMY/CALCE PAPER presented at the 2013 RAMS conference event mentioned in this podcast– “Reliability Prediction – A Continued Reliance on a Misleading Approach” . This is a government document that is in the public domain and should be distributed a read by any engineer that believes failure prediction methodology is useful or beneficial during product development.
Kirk suggests in root cause analysis to compare a failed part to a new off-the-line part. Leveraging contrast between a failed part and a good reference part is powerful, especially when the differences between the failed part and reference part are minimized. When it’s possible, I would compare the failed part to another part built at the same time that also went to the field, ideally to the same application or customer (in automotive, there are generally plenty of “No Trouble Found” returns).
Working only with failed parts has the risk of missing the root cause for something that just looks bad. Engineers see the bad looking thing and decide that is the root cause. However, if they looked at a part of similar pedigree (same model, same build lot, same application, similar time in use,) they might find that the functioning part has the same bad looking thing–what they want to be the root cause isn’t. Conversely, it could provide much more clear evidence that the bad looking thing is really the bad thing.
I think it is very important to emphasize in root cause analysis to not just look at the failed parts–you should look at functioning parts, too. The more similar the failed and functioning parts are, the better.
Thanks Keith for your comment. I agree with you wholehearted. You make an excellent point. Also, I would compare the parametric response of other parts from the same lot when stressed during a HALT evaluation. This can be especially true for no fault found parts that may not really have the operating margin that the part did during the development stage (lot to lot variance)
Thanks again for listening and your input.
Kirk