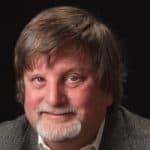
Testing Without Knowing Mechanisms
Abstract
Kirk and Fred discussing how to test a new product without knowing the specific mechanisms that will be a possible weakness, and reliability issue in the field
Key Points
Join Kirk and Fred as they discuss accelerated testing of mechanical systems and accelerated testing
Topics include:
- Care must be used in accelerating the testing by increasing the number of use cycles, as it may result in changing the physics of wear, as with a kitchen blender not letting the unit cool down between power cycling events.
- Those new to HALT methods should always keep the testing simple with one stress applied at a time making the failure analysis easier to understand
- Sometimes the test setup is not a valid simulation, such as the USB insertion testing failure that was using a simple mechanical plunger that did not simulate how a human hand would have a felt the mechanical resistance that would prevent the severe mechanical damage seen.
Enjoy an episode of Speaking of Reliability. Where you can join friends as they discuss reliability topics. Join us as we discuss topics ranging from design for reliability techniques to field data analysis approaches.
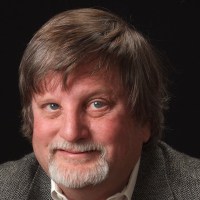
- Social:
- Link:
- Embed:
Show Notes
For more information on the newest discovery testing methodology here is a link to the book “Next Generation HALT and HASS: Robust design of Electronics and Systems” written by Kirk Gray and John Paschkewitz.
Kirk and Fred, it’s an interesting topic and thank you for bringing up the discussion. although the discussion so far has been focused on wearout failures, random failures may want to be considered also, as they are in theory the one that determines reliability of a product in operation. the wearout failures determine lifetime and, yes, they are accelerated based on known mechanisms. but random failures, generally speaking, happen earlier and are identified by being operated in simulated or actual usage conditions. In addition, the quantitative measure of random failures, i.e. MTBF or failure rate, is usually determined by accumulated test time of samples, which means that a number of samples with limited test duration for each one may need to be tested to gain knowledge about how a product fails, as well as confidence on an expected MTBF level. based on this gained knowledge of failures, acceleration can then be considered to determine lifetime.
Thanks for your comment Jason.
Random failures in my experience are mostly due to misuse or latent defects introduced in manufacturing and vary throughout the manufacturing cycle. This is why any failure in testing should have a deep RCA to determine the cause.
MTBF is a poor metric for reliability. See the website http://WWW.NOMTBF.COM for more reasons why it should not be used.
Hello Kirk and Fred. Long time.
There is an argument now that there is no such thing as a random failure, since any failure must have a failure mode.
Worth thinking about?
Thanks Dave, and yes it has been a long time since we heard from you.
I agree that there not really a “random” failure as you are right that there is a assignable cause to every failure mode and mechanism.
As I believe that there is no such thing as infant mortality except with humans, and it is dismissive as it is implied that “it’s JUST infant mortality” in some of the components and to be expected , and the root cause not addressed or corrected.
Thanks for listening.