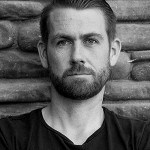
Proper Use of Cpk
Abstract
Chris and Fred discuss what ‘Cpk’ and other ‘capability indices’ mean … especially when it comes to reliability. Never heard of this or want to learn more? Listen to this podcast!
Key Points
Join Chris and Fred as they discuss one of the best-known Capability Indices called ‘Cpk.’ It is a metric used in manufacturing a lot. But it is often seen as a ‘quality’ thing and not a ‘reliability’ thing. But in practice, you can’t talk about one without talking about the other. If a product fails because of a design flaw versus a manufacturing flaw … does your customer care?
Topics include:
- What is ‘Statistical Process Control (SPC)?’ SPC is all about keeping processes in control. Imagine being a passenger in a taxi where the steering wheel is damaged to the extent that the driver has to work very hard, turning the steering wheel left and right just to go straight. Even if your taxi is (somehow) staying on the road … would you say that the taxi is in-control? Ideally if we detect play in the steering wheel of our car, or a loose pedal, or a weird noise coming from the engine … we take our car to the garage to get repaired. This is what SPC is all about. It is sometimes hard to detect when a manufacturing process is starting to do something unexpected, so SPC focuses on some statistics and metrics that if we measure and organize in a specific way, help us give us much EARLY WARNING as possible that something is about to go wrong – even if everything is in specification now.
- Let’s talk about ‘workarounds.’ Workarounds are a necessary part of life. But they can be used so often that they guarantee long term failure. We often use workarounds when we let something degrade to a crisis. This means that there might be an issue that stops production entirely, so there is pressure from management to fix the crisis quickly. Workarounds are quick and (ideally) shortterm. They are also the only solution you have if you have allowed your process to degrade to a point that fixing it now costs millions of dollars. But if we had fixed it when we first received early warning, it would have cost hundreds of dollars. Think about the taxi … is it cheaper to fix the steering pinion when we detect some play, or panel beat the vehicle back together after it has wrapped around a tree because the driver couldn’t control it anymore?
- What is ‘Cpk’ anyway? Cpk is a ‘capability index’ which is a measure of the extent to which the natural variation of your process lies within specification. The premise is that Cpk is based on an in-control process (if the process is out of control, then it will be changing unexpectedly all the time). A higher Cpk implies there is less variation outside of specifications. So it is a really good way of defining the quality of a process.
- What ‘Cpk’ should I be aiming for in my process #1? Depends who you ask! Some say that we should be aiming for Cpk goals of 2.0, or sometimes 1.33 if it is an existing process, or 1.5 if it an established process, and plenty of others. The problem is that any of these could still mean that you don’t meet your quality and reliability goals. For some organizations, 1.33 is enough. For others, 2.0 is not.
- What ‘Cpk’ should I be aiming for in my process #2? You need to find your quality goals and then allocate these goals down to your individual processes. So there is a bit more to it! And this includes working out which processes you want to focus on.
- And get your specifications right. Including tolerances. Your manufacturing engineers will thank you!
Enjoy an episode of Speaking of Reliability. Where you can join friends as they discuss reliability topics. Join us as we discuss topics ranging from design for reliability techniques to field data analysis approaches.
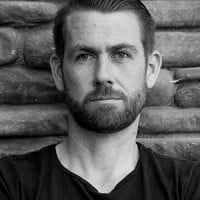
- Social:
- Link:
- Embed:
Related Topics
SOR 738 Design Use of Cpk(Opens podcast in a new browser tab)
Leave a Reply