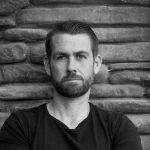
Improving or Suing
Abstract
Chris and Fred discuss whether you want to lay blame (i.e. sue) or improve reliability? Don’t be confused … accountability is important. But that doesn’t replace everyone ‘owning’ the end result.
Key Points
Join Chris and Fred as they discuss how many organizations treat reliability engineering activities as being able to work out ‘who stuffed up.’ Which ideally … is never me …
Topics include:
- Think about suppliers and root cause analysis. Many root cause analysis activities conclude in finding that the supplier was at fault. And then we stop. Why? Because it was their fault. But so what? What good is that moving forward? How do we stop this from happening again? We don’t care! It is there job to do a better job!
- A root cause is something you can address. If you can’t … it is an environmental constraint. If you can’t influence the quality of your supplier products (and just allocating blame is not influencing anything in a positive way) then it MUST be an environmental consideration. If your suppliers are ‘rubbish’ then it is up to you to incorporate this reality into your design (for example). Maybe you need to incorporate redundancy. Introduce environmental chambers to keep the part in ‘optimal’ temperature and humidity bands. Otherwise … all you are doing is admiring a problem.
- But we can’t influence supplier quality … can we? Of course we can! We know (for example) that there are many products and systems manufactured by different organizations which have well-earned reputations for reliability. But … they rely on their supplier networks as much as anyone else. So how can this be? The organizations who do this the best are those that set up collaborative and transparent relationships where issues are identified as early as possible and then addressed by the ‘right’ group of people. Which might be in the supplier or manufacturer’s organization … at the same time.
- The reality is that the person who ‘created’ the problem might not be the right one to ‘solve’ it. What? Think of a medical device company that is trying to create a wonderful new testing machine that relies on microfluidic behaviour at scales that are too small for us to see. Let’s say one of the suppliers manufactures a plastic insert that is supposed to partition fluids into tiny wells that are nanometres deep. Initial prototype testing shows that for whatever reason, the fluid being examined (which usually includes a sample of blood to test for viruses and things like that) is not ‘staying’ in these wells. Is this the supplier’s fault? Who cares … it should be up to the design, pumping, chemical, manufacturing AND suppliers to work together to see if tweaking flow rates, chemical compositions, and of course well dimensions will solve the problem. A multi-pronged approach is faster, more efficient and will find the cheapest way of solving the problem!
Enjoy an episode of Speaking of Reliability. Where you can join friends as they discuss reliability topics. Join us as we discuss topics ranging from design for reliability techniques to field data analysis approaches.
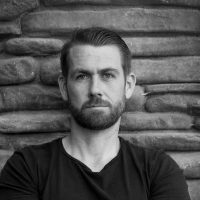
- Social:
- Link:
- Embed:
Related Topics
Failure Analysis: The Key to Learning From Failure(Opens article in a new browser tab)
Thanks for the inspiration. What are the consequences if any of not doing the best you can?
People say: We met the specs. We doing as badly as best in class. We followed the standard. We met the benchmark.
Imagine if Theranos people knew d test output/d component performance drift(age)? I did for Abbott hemoanalyzers. (Abbott at that time was also trying to minaturize hemoanalyzers from giant desktop machines to laptop size.)
That’s what happens when the culture of an organization doesn’t allow people to make the wonderful connection between quality/reliability and reduced time/costs. It becomes a race to a milestone.