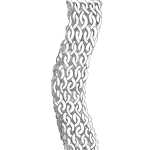
Routine Reliability
Abstract
Dianna and Fred discussing routine reliability from a listener’s question: when creating a reliability plan for a project, how do we separate the routine and unique parts of reliability activities?
Key Points
Join Dianna and Fred as they discuss reliability planning: the technique and frameworks used to achieve reliability objectives.
Topics include:
- why having a process to create a plan is much better than trying to use a standard plan
- some traps when trying to standardize
- packing for travel, root cause analysis
Watch for Fred and Carl’s new book about reliability planning, to be released soon!
Enjoy an episode of Speaking of Reliability. Where you can join friends as they discuss reliability topics. Join us as we discuss topics ranging from design for reliability techniques to field data analysis approaches.
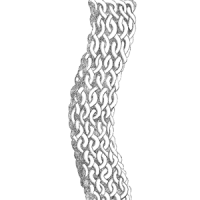
- Social:
- Link:
- Embed:
Show Notes
Have a standard process for how to CREATE a reliability plan. Don’t have a standard reliability plan. We first need to ask ourselves “why”? What is it we need to know this time? Then, what do we need to do?
Some questions to ask to put together a plan to achieve reliability objectives:
- What are we trying to achieve?
- What information do we know or don’t know?
- What are our constraints?
- How are we going to get that information to inform decisions?
- How do we monitor it?
Review a previous plan for lessons learned, to incorporate those into your new plan.
Some traps to be aware about:
- We tend to get asked, “How many samples do I need?” Instead, we should ask, “What type of information do we need to extract from samples?”
- Collecting test results out of habit without really doing anything with the results.
- Doing tests because we have the equipment and because that’s how we’ve always done it, but not really getting the answers we need to achieve those real reliability objectives.
Hi Fred and Dianna.
I like and agree with your comments that the reliability and quality test plan should be risk-based and not just a standard list of tests run on every new design. We use a risk-based quality test plan where we start with a meeting with the engineers and ask questions like “how is this new design similar and different from past designs? What do you see as the biggest risk? Then we rank each facet of the design, mechanical, electrical, software, test, etc., on a scale from 1-10, low to high risk. Any high risks are then detailed out by component. finally, we start the test plan based on this risk assessment.
I enjoyed your podcast and your anecdotes about repeating tests just for the sake of using our equipment or because that’s the way we’ve always done it. I can relate!
All the best,
Bob