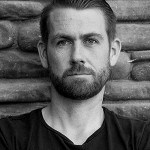
An ALT Design Question
Abstract
Chris and Fred discuss an ALT or Accelerate Life Test Design Question. We love these podcasts … as we are directly answering a question from one of our listeners. Interested in hearing a response to a real-world question from a listener?
Key Points
Join Chris and Fred as they discuss helping out one of our listeners through a problem he is experiencing regarding a ‘thermal-shock’ test in the order of 1 000 000 cycles. There are a few things to unpack here … so let’s go.
Topics include:
- Can we just focus on the ‘b50′? What is the ‘b50′? It is the median time to failure of something like a bearing or other things that fail due to damage being accumulated through repeated stresses or cycles. But … is the ‘b50′ the right metric? For most decisions, it isn’t. It won’t help you work out (for example) how long it will take before 5 % of your products fail. This is a much more common question that needs to be answered.
- Do we need three different stress levels? For ALT … yes. This is because ALT is based on a model that you need to pick to help convert time spent at accelerated stresses back to normal operating conditions. Many organizations simply find a model they like in a textbook and go with it. Finding a model in a textbook is a great first step … but you need to confirm that it works for your product, which has its own set of failure mechanisms.
- Then Chris and Fred talk about their different take on the samples, stress levels and so on. It is very important to make sure that by increasing stresses (like temperature) you don’t change the state of the product. You don’t want to (for example) melt it. But even if you don’t melt it, there are things that temperature can do at a microscopic level that will change the way things fail. Fred likes stacking the samples closer to the use case level. Chris … not so much. Listen to this podcast to hear why?
Enjoy an episode of Speaking of Reliability. Where you can join friends as they discuss reliability topics. Join us as we discuss topics ranging from design for reliability techniques to field data analysis approaches.
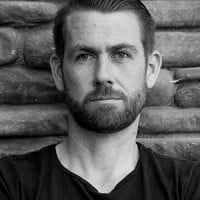
- Social:
- Link:
- Embed:
Related Topics:
How to Create an ALT Plan(Opens podcast in a new browser tab)
Hi Fred and Chris.
Really enjoyed your discussion on ALT and answering Johan’s question about thermal shock failure.
I heard Chris mention that he is creating a class on ball-bearing reliability. Well it just so happens that I am trying to develop an ALT for fan motors that I need to demonstrate a 3-year life minimum where the motors will be running 24/7/365. Doing some reading on fan motor reliability, the motors usually fail first due to bearing life and second due to insulation resistance or winding failures. Typical reasons for bearing failures are bearing grease failure or breakdown. I have to believe there is an ALT design already developed by someone that I can trust will measure the reliability of these motors, but I cannot find one after several hours on Google. I was planning on doing a 5×3 test, running 5 motors each at 3 different temperatures and 3 different loads (2 accelerating factors, heat, and load). Choosing the temperatures and loads is the challenging part. I assume that I want to stay under the bearing grease temperature where the grease turns to a liquid and runs out of the bearing. I also assume for temp and load that I want to stay within the manufacturer’s recommended operating limits or maybe only exceed them by 10-20% at most, assuming there is some design margin.
Listening to you and Fred, I liked Fred’s idea of running a higher sample size at the lowest level. So maybe I should test at least 10 and maybe 20 motors at the lowest level. My other challenge with this test is that I need results within 8 months, so the lowest level needs to demonstrate some failures.
If you have any advice, data or models that you can share it would be greatly appreciated.
Best regards,
Bob
Bob,
This is a really well explained scenario. In regard to ball bearing ALT, there is some stuff out there but not a lot. And the reason is that bearing life is usually defined by spalling, which is a very particular form of fatigue that is unique to ball bearings where rolling elements repeatedly roll over what will always be an imperfect surface.
So when it comes to accelerating fatigue, temperature (directly) is not (usually) a good stress. That said, if you REALLY understand the mechanics of your ball bearing, what increasing the temperature can do is decrease the initial clearance, meaning that when everything heats up the balls are now ‘expanded too big’ and then impart additional stress on the bearing races. There is no reason why you can’t use this approach … if you really know the mechanics of your bearing.
You are 100 % correct in that you cannot increase temperature so much that the grease changes its state. That invalidates the test.
So increasing loads either directly (or indirectly through some increase in temperature) might be the way to go.
So how to increase the loads (without temperature)? There are a few that you probably have in mind, and a novel approach can be found here chrome-extension://efaidnbmnnnibpcajpcglclefindmkaj/https://scholar.uwindsor.ca/cgi/viewcontent.cgi?article=9331&context=etd where gyroscopes can be used.
But regardless of the approach, you will need to validate the model for your bearings. Which means you need to have those multiple stress levels.
And even though I feel insulted that you are going with Fred’s suggestion and not mine(!) … I think you are asking some really, really good questions, which shows you know what you are looking for, and how even a little bit of research can pay off.
Let me know if this does or does not help your journey.
Chris