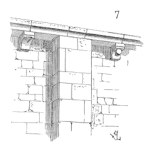
How Root is the Cause?
Abstract
Carl and Fred discuss the broad subject of identifying root causes and how deep to go. It’s not as simple as getting to the “root.”
Key Points
Join Carl and Fred as they share experiences in root cause analysis and how it is applied in various reliability engineering methods.
Topics include:
- There is no single method for identifying root cause; it depends on the analysis being used.
- Root cause for Design FMEA goes down to the design deficiency level; whereas root cause for Supportability FMEA goes to the maintenance-actionable level
- Ask: at what level is it appropriate to take action?
- Fix problems now, and systemically, both
- Some root cause analyses continue to the human level, ask: what is the human system and how does human error contribute to the root cause?
- The level of the analysis should be agreed on before beginning
- What about multiple causes, is there more than one root?
- Is the human deficiency part of the root cause for Design FMEA?
- Ask: where are you going to take action? what part of our process enabled this to occur?
- Eight Disciplines (8D), step 4 is determine, identify, and verify root causes
- Severity and occurrence are both part of risk analysis
- Don’t merely blame the supplier or operator
- The root cause needs to be something you can remedy
- One of aspects of root cause is to ask if resources are available to fix the cause
Enjoy an episode of Speaking of Reliability. Where you can join friends as they discuss reliability topics. Join us as we discuss topics ranging from design for reliability techniques to field data analysis approaches.
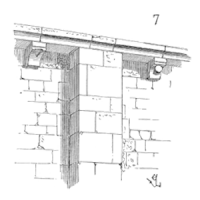
- Social:
- Link:
- Embed:
Show Notes
Leave a Reply