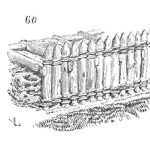
The Most Common FMEA Mistakes and How to Avoid Them – Part I
Abstract
Carl and Fred discuss some of the most common mistakes made by FMEA practitioners and how they can be avoided. In this episode, 4 of the most common mistakes are discussed.
Key Points
Join Carl and Fred as they discuss common FMEA mistakes and how to turn them into quality objectives.
In this episode, they discuss 4 common mistakes and the corresponding quality objectives. In the next podcast, 6 other common mistakes are discussed.
Mistake No. 1: design/process improvements
A review of FMEA applications across industries shows some FMEAs drive ineffective actions or no action at all.
Some design FMEAs drive mostly testing, while some process FMEAs drive mostly controls. FMEA’s failure to drive product or process improvements is a mistake.
FMEA quality objective No. 1: The FMEA drives design improvements (design FMEA) or manufacturing or assembly process improvements (process FMEA) as the primary objective.
Mistake No. 2: design verification or process control plans
Some organizations miss the opportunity to improve their design verification plan (DVP) or process control plan (PCP) based on the failure modes or causes from the FMEA.
The result is inadequate product testing or PCPs. Failure of the FMEA to improve test and control plans is a mistake.
FMEA quality objective No. 2: The DVP considers the failure modes from the design FMEA. The PCP considers the failure modes from the process FMEA.
Mistake No. 3: interfaces
Empirical data show at least 50% of field problems can occur at interfaces between parts and subsystems or between the system and environment.
Similarly, many manufacturing or assembly problems occur at the interface between operations or beyond operations, such as while transporting materials, receiving incoming parts or shipping.
Some practitioners miss these interfaces. Not including interfaces in design or process FMEAs is a mistake.
FMEA quality objective No. 3: The scope of the design FMEA includes interface failure modes in both FMEA block diagram and analysis. The scope of the process FMEA includes inter-operation failure modes, such as transfer devices, and incoming parts and shipping, in both process flow diagram and analysis.
Mistake No. 4: lessons learned
“Those who don’t know history are destined to repeat it.” Edmund Burke
Some organizations do not provide links between FMEAs and field data (in design FMEAs) or manufacturing data (in process FMEAs). It takes concerted effort to integrate problem resolution databases with the FMEA. A lack of integration can cause serious problems to be repeated. Disconnect between the FMEA and information from the field or plant is a mistake.
FMEA quality objective No. 4: The FMEA considers all major lessons learned (from in-service warranties, customer service databases, recall campaigns, prior manufacturing or assembly problems and others) as inputs to failure mode identification.
Enjoy an episode of Speaking of Reliability, where you can join friends as they discuss reliability topics.
Join us as we discuss topics ranging from design for reliability techniques to field data analysis approaches.
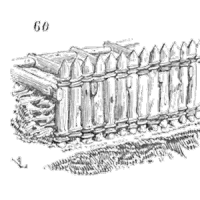
- Social:
- Link:
- Embed:
Show Notes
Carl’s FMEA website with many articles on FMEA and downloadable FMEA aids: www.effectivefmeas.com
Article: Good FMEAs, Bad FMEAs, What’s the Difference?
Article: Practice Auditing an Actual FMEA
Failure mechanisms are the processes by which physical, electrical, chemical and mechanical stresses induce failure. Knowledge of the failure mechanisms that cause product failure is essential to design and qualify reliable products. The standard Failure Modes and Effects Analysis (FMEA) and Failure Modes, Effects and Criticality Analysis (FMECA) procedures do not identify the product failure mechanisms and models, which limits their applicability to provide a meaningful input to critical procedures such as virtual qualification, root cause analysis, accelerated test programs, and to remaining life assessment. Failure Modes, Mechanisms and Effects Analysis (FMMEA), enhances the value of FMEA and FMECA by identifying high priority failure mechanisms and failure models. High priority failure mechanisms determine the operational stresses, and the environmental and operational parameters that need to be controlled. Models for the failure mechanisms help in the design and development of a quality product
Hello Hilaire.
I appreciate your comments about the value of including failure mechanisms in FMEA. I completely agree!
As I wrote in my reply to your earlier comments on the same subject, I always teach that higher-risk issues in an FMEA must be taken to root cause and corresponding failure mechanisms. And I make this point in detail in my book. I also have a section in chapter 15 of my book on FMMEA, and have worked with colleagues at CALCE on FMMEA papers and dialog. FMMEA does exactly as you say.
Actually, some of the FMEA standards do discuss the value and application of Failure Mechanisms in FMEA procedure. For example, one of the most well-known FMEA references is AIAG 4th edition. On page 39 there is a section on “Potential Mechanism(s) of Failure Mode”, which defines failure mechanisms and how to use them in FMEA procedure. However, as you point out, the FMEA standards do not discuss the modeling of failure mechanisms, which is important.
We need to keep emphasizing the proper application of failure mechanisms in FMEA, and I appreciate your bringing it up.
Carl