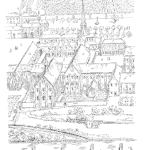
The Most Common FMEA Mistakes and How to Avoid Them – Part II
Abstract
Carl and Fred discuss to discuss the most common mistakes made by FMEA practitioners and how they can be avoided.
Key Points
Join Carl and Fred as they continue to discuss common FMEA mistakes and how to turn them into quality objectives.
In this episode, they discuss 6 other common mistakes and the corresponding quality objectives, bringing the number of mistakes discussed in the two podcasts to the ten most common mistakes.
Mistake No. 5: high-risk failure modes
Although organizations define risk using different criteria, failure to address all high-risk failure modes can result in potentially catastrophic problems or lower customer satisfaction. Failure of FMEA to address all high-risk failure modes is a mistake.
FMEA quality objective No. 5: The FMEA addresses all high-risk failure modes, with effective and executable action plans.
Mistake No. 6: level of detail
Some FMEAs are too detailed in their analysis, which makes it difficult to focus on areas of higher risk. Some FMEAs aren’t detailed enough, which makes it difficult to determine the root cause and effective corrective actions. Having the wrong level of detail in the analysis is a mistake.
FMEA quality objective No. 6: The FMEA provides the correct level of detail to get to root causes and effective actions.
Mistake No. 7: timing
Many organizations conduct FMEAs late, and this reduces their effectiveness. FMEAs should be completed according to design or process freeze dates in accordance with the product development process. Performing FMEAs late is a mistake.
FMEA quality objective No. 7: The FMEA is completed during the window of opportunity from which it can most effectively affect the product design or manufacturing process.
Mistake No. 8: team
Some FMEA teams do not have the right experts as members. Some FMEA team members just sit in their chairs if they show up at all and don’t contribute to team synergy. FMEAs having inadequate team composition and participation is a mistake.
FMEA quality objective No. 8: The right people, adequately trained in the procedure, participate on the FMEA team throughout the analysis.
Mistake No. 9: documentation
There are hundreds of ways to do FMEAs wrong. Some organizations do not encourage or control proper FMEA methods.
Or, they copy old FMEAs and don’t adequately address changes, such as new technology or new applications. Training, coaching, and reviews are necessary for success. Use of improper FMEA procedures is a mistake.
FMEA quality objective No. 9: The FMEA document is completely filled out by the book, including action taken and final risk assessment.
Mistake No. 10: time use
Some organizations mandate FMEAs, but that doesn’t ensure the time spent on them is productive.
Pre-work must be completed, meetings must be productive and high-risk issues must be resolved. Ask the FMEA team whether their time was well spent, and take action to address shortcomings. Inefficient use of time is a mistake.
FMEA quality objective No. 10: Time spent by members of the FMEA team is an effective and efficient use of time with a value-added result.
Enjoy an episode of Speaking of Reliability, where you can join friends as they discuss reliability topics.
Join us as we discuss topics ranging from design for reliability techniques to field data analysis approaches.
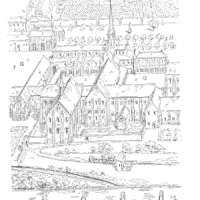
- Social:
- Link:
- Embed:
Show Notes
Carl’s FMEA website with many articles on FMEA and downloadable FMEA aids: www.effectivefmeas.com
Article: Good FMEAs, Bad FMEAs, What’s the Difference?
Article:Â Practice Auditing an Actual FMEA
Leave a Reply