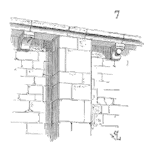
When to Do FMEAs
Abstract
Carl and Fred discussing when FMEAs should be done to support product development projects. FMEAs take time and cost money to support, and should be done when a certain level of risk can be effectively addressed by the FMEA procedure.
Key Points
Join Carl and Fred as they discuss selection criteria for FMEA projects.
Topics include:
- The value of FMEAs
- Guidelines for when to perform FMEAs
- FMEA project selection criteria
- A techinique called “preliminary risk assessment”
- When FMEAs are not needed
Enjoy an episode of Speaking of Reliability. Where you can join friends as they discuss reliability topics. Join us as we discuss topics ranging from design for reliability techniques, to field data analysis approaches.
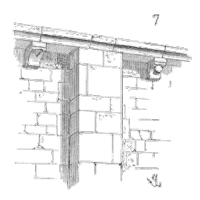
- Social:
- Link:
- Embed:
Show Notes
Preliminary Risk Assessment (excerpt from chapter 4 of Effective FMEAs)
“Short of doing FMEAs on all subsystems and components, which can be very expensive and time consuming, there needs to be a way to prioritize potential FMEA projects, to help identify which FMEAs to do. One way to do this prioritization is Preliminary Risk Assessment. Here is a simple procedure for performing a Preliminary Risk Assessment:
“Open up a simple spreadsheet or use FMEA software that supports Preliminary Risk Assessment. In the first column, list the bill of materials or the complete system hierarchy (listing of the subsystems and components). Across the top of the spreadsheet put the risk criteria used to prioritize the risk of the subsystems and components, as described below.
“Develop the company-specific risk criteria for use in assessing risk for each item in the bill of materials. For example:
- Risk identified by System or Concept FMEA (Does the System or Concept FMEA point towards risk in the item?)
- Potential for safety issues (What is the degree of safety risk associated with the item?)
- New technology (What is the degree of new technology being introduced with the item?)
- New applications of existing technology (What is the level of new application for existing technology with the item?)
- History of significant field problems (What level of field problems has been associated with the item or similar items?)
- Potential for important regulation issues (What level of government regulation is associated with the item?)
- Mission-critical applications (To what degree can failures with the item bring about loss of primary mission?)
- Supplier capability (What is the risk associated with the supplier of the item?)
“Note: These risk criteria can and should be tailored to the circumstances of an individual company or organization and applied to each item in the Bill of Materials.
“The next step is to rank each risk criteria column for each row in the system hierarchy on a scale of risk, such as high, medium, or low, or 1 to 5. In other words, assess the risk for each item in the Bill of Materials according to the risk criteria.
“The final step uses simple arithmetic to multiply the cells in each row to obtain a risk index number for each of the subsystems or components in the system hierarchy. This index can then be used as input to the FMEA selection decision.”
very good, thanks!