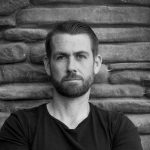
6 Sigma and Reliability
Abstract
Chris and Fred discuss what the idea of ‘6 sigma’ means for reliability. What is ‘6 sigma?’ Is it a buzzword? There are lots of different ideas on what ‘6 sigma’ is. We are always on the look out for amazing new things that are going to help us do reliability stuff. Want to learn more? Listen to this podcast.
Key Points
Join Chris and Fred as they discuss ‘6 sigma.’ What is ‘6 sigma?’ Well … it’s complicated. Because many different people have different ideas on what it means.
Topics include:
- What is ‘6 sigma?’ It is an idea that is based on manufacturing components that are so far inside design tolerances that they won’t ever approach ‘unsatisfactory’ dimensions that the ultimate product will be very reliable. And it can also be looked at as designing something that is so robust that manufacturing inaccuracies will have a limited effect on overall reliability.
- But what about other ideas? Like ‘6 sigma’ being a methodology where you create a team to solve a problem. How is this a ‘6 sigma’ thing only? It’s not!
- So where does the title of ‘6 sigma’ come from? The idea is that the normal distribution (bell curve) can be described by its standard deviation – something we often represent with the Greek letter ‘sigma.’ So the idea is that the variation in the dimensions of something you are manufacturing IS modeled by a bell curve, and that we want tolerances (or ‘bad’ dimensions) to be ‘6 sigmas’ away from the mean value. BUT … not everything is modeled by a bell curve – especially at the extreme values that matter when it comes to things being out of specification. And because of these assumptions and underlying statistics, people who can’t ‘handle’ the statistics simply assume statistical principles … and go back to building teams to solve problems.
- So how does ‘6 sigma’ relate to reliability? Well, it is great if ‘6 sigma’ means you work out how your thing can fail (like a FMEA), identify where manufacturing will contribute to failure, and then set tolerances to prevent this, then ‘6 sigma’ or any other school of thought that focuses on high-quality manufacturing will contribute to reliability. But if ‘6 sigma’ is reduced to a philosophy for creating teams that solve problems … then what is so special about it?
Enjoy an episode of Speaking of Reliability. Where you can join friends as they discuss reliability topics. Join us as we discuss topics ranging from design for reliability techniques to field data analysis approaches.
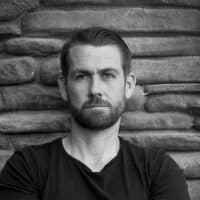
- Social:
- Link:
- Embed:
Show Notes
Good topic!! I became a SS Black Belt as part of an internal certification process. The methodology and tools helped a lot to solve reliability problems and I believe it provides the DMAIC methodology provides a great framework to support reliability improvement !
Thanks for the note Luiz and for listening to the episode.
I agree that the structure for problem solving does help many realize improvements in reliability performance. I think it should be more than just the DMAIC process, and include the connection of design tolerance analysis to the process capability information for parts and features.
cheers,
Fred
Thanks for your input Luiz!
There are lots of benefits that DMAIC can bring to an organization. I suppose my note of caution is that DMAIC is a tool … and like all tools, they have different purposes. DMAIC isn’t the answer for everything, but is a good answer for some things.
Chris
Great topic. Many thanks. I work in the airline reliability environment. Am a Green Belt. The reliability domain in my airline world is very ‘narrow’ and almost confined to just 1 or 2 specialists. Got my Green Belt, by luck, from an initiative from an external resource. I ‘self’ apply DMAIC techniques in the problem detection and investigation process. I only present the end result solutions to management without going into the DMAIC process as it kind of ‘overwhelms’ the meetings. In the airline environment, there is very little one can do to designs except to feedback to the OEMs. The design fixes take a long time and the operator has to manage the problem in the meantime. I often take the approach of ‘within my zone of control’ solutions. These include the domains of maintenance programs, more data collection, warranties, training etc. The DMAIC process provides a very structured process. It ensures vital phases are not missed. The rigor discovers many problem aspects including hidden ones and triggers many solution options to contain the problem whilst waiting for design solutions if they ever come!
Selva
Hi Selva,
thanks for the note and story on how despite the odds you are able to successfully use DMAIC.
cheers,
Fred